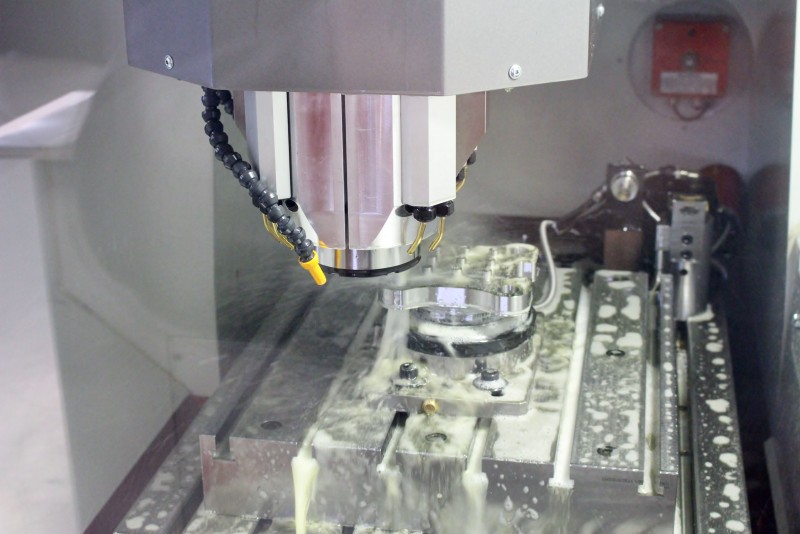
Optimale verspanende bewerkingen vergen een uitgebalanceerd proces. Het gaat niet alleen om de machine: gereedschap, koelstrategie en CAM-programma moeten in balans zijn. Wat zijn de trends op deze gebieden?
Machines multitasken. Dat is een trend die al langer zichtbaar is, met name in de combinatie draaien en frezen op één machine. Het multitaskingconcept van Mazak, dat met de Integrex deze trend heeft gezet, wordt veelvuldig gekopieerd. Dit leidt er ondertussen toe dat veel kubische delen worden gemaakt uit stafmateriaal op dergelijke multitasking machines. Index heeft in dit kader eind vorig jaar de nieuwe versie van de G220 op de markt gebracht.
Ook Starrag heeft zo’n machine ontwikkeld, de LX021. Een van de voordelen van deze opzet is dat je de productie vrij gemakkelijk kunt automatiseren zonder een robot bij de machine te zetten. Via een stangenlader wordt de machine beladen, door de overnamespil en de aangedreven gereedschappen worden de doorgaans kleine producten compleet in één opspanning afgewerkt. Vooral als het om kleine componenten gaat is dit een aantrekkelijk concept. Doordat de machines gebaseerd zijn op een horizontale draaibank, is de spanenval optimaal. Sommige fabrikanten gaan zover dat ze in de machine een eenvoudige grijperarm installeren die het product uitneemt en op een transportband legt. Index doet dat bijvoorbeeld bij de GX220.
Een-tweetje
Machinebouwers gaan echter verder dan alleen draaien en frezen combineren in één machine. Dymato liet tijdens de laatste TechniShow de nieuwe RXP 801Z2 van Röders zien, een bewerkingscentrum dat hogesnelheidsfrezen combineert met slijpen . Hierdoor kan men de voordelen van beide technieken in één werkstuk benutten. Dit moet de doorlooptijd ten goede komen. De machine kan binnen 2 µm nauwkeurig bewerken.
Monforts Werkzeugmaschinen heeft de Laserturn al enkele jaren geleden voorgesteld. Ondertussen is de machine productierijp. Dacht de machinefabrikant eerst nog aan het gecombineerd laser-draaien van materialen zoals keramiek, ondertussen kiest men ervoor om de laser in te zetten voor het harden van de werkstukken. Dit blijkt in de markt gewild te zijn. Het gaat hier overigens niet om door en door harden, maar enkel een deel van het werkstuk waarop een slijtvaste laag nodig is (1 tot 2 mm diep, hardheid 60 HRc). Doorlooptijdverkorting is resultaat van deze combi, omdat het werkstuk na het draaien niet nog apart gehard hoeft te worden, al dan niet extern.
3D metaalprinten
Andere combinaties van bewerkingen zijn er ook al. Toyoda bouwt bijvoorbeeld een machine voor het combineren van draaien en slijpen in één opspanning. En op het gebied van 3D metaalprinten lijkt het dat DMG Mori Seiki een richting aanduidt met de Lasertec 65 3D. Inmiddels integreert ook Mazak additive manufacturing in een verspanende machine, net als Matsuura. De meningen hierover lopen uiteen. Sommigen geloven in de combinatie, andere wijzen erop dat in zo’n hybridemachine één technologie – lasersmelten of verspanen – niet gebruikt wordt als de andere techniek is ingeschakeld. Overigens is DMG Mori Seiki momenteel nog de enige die deze machine in Europa verkoopt, de andere twee doen dat nog niet. Wel heeft onlangs het Brits-Amerikaanse Hybrid Manufacturing Technologies de eerste International Additive Manufacturing Award gewonnen met een hybridekit voor bestaande CNC-bewerkingscentra. Deze kunnen met deze kit – met onder andere een laserunit en besturingssoftware van Delcam – omgebouwd worden naar bewerkingscentra met additive manufacturing mogelijkheden.
Koelsmeren
Koelsmeermiddelen drukken hun stempel op de prestaties van een frees- of draaimachine. Misschien is dit wel dé onderschatte factor in de verspaning. Hoe dichter de emulsie bij de snijkant van het gereedschap wordt gebracht, des te effectiever is de werking. Een duidelijke trend op dit vlak is de inzet van hogedruk koeling. Bewezen is dat dit voor langere standtijden zorgt en betere oppervlakken. Het gaat echter niet alleen om de druk.
Iscar heeft met een Duitse universiteit onderzoek gedaan naar de samenhang tussen druk en volumestroom. Hieruit blijkt dat veel koelsmeermiddel niet per se tot betere resultaten leidt. Een te grote volumestroom is minder effectief omdat een groot deel van de emulsie aan de onderkant van de spaan belandt zonder daadwerkelijk in het snijvlak te koelen. Het onderzoek liet zelfs zien dat een hogere volumestroom bij een hogere druk tot een daling van de standtijd van het gereedschap leidt.
Een veelbelovende ontwikkeling die nog niet echt doorbreekt, is de cryogene koeling, met CO2 of stikstof. Er wordt volop onderzoek naar gedaan, omdat dit met name effectief lijkt bij het bewerken van materialen zoals titanium, waarbij de temperaturen hoog oplopen en vooral door het gereedschap worden opgenomen. Dat leidt tot overmatige slijtage. Omdat de luchtvaartindustrie meer composiet gaat gebruiken, zal ook het aandeel titanium toenemen omdat dit materiaal beter kan worden gecombineerd met vezelversterkte kunststoffen dan aluminium. De productiviteit bij het bewerken van titanium moet dus omhoog. Stikstof werkt in theorie goed, maar is in de praktijk lastiger toe te passen omdat het behoorlijke aanpassingen aan de machine en de installatie vergt. CO2, vaak in de vorm van droogijs, is een alternatief dat eenvoudiger toegepast kan worden. Het vloeibare stikstof wordt bij kamertemperatuur tot in het gereedschap gebracht en koelt pas fors af zodra het uit met de buitenlucht in contact komt.
Een combinatie van CO2 koelen met minimaalsmering is een tussenvorm die sommige fabrikanten, zoals Hermle, al aanbieden. Walter heeft hiervoor een speciale gereedschappenlijn ontwikkeld. Ook Haimer speelt op deze trend in door een Cryo-gereedschaphouder met twee inwendige kanalen te ontwikkelen, een voor de toevoer van CO2 en een ander om het aerosol (olie- en luchtmengsel) naar het gereedschap te brengen.
Gereedschappen
Bij de gereedschappen zoeken fabrikanten de oplossing voor langere standtijden en hogere spaandebieten in de afstemming van substraat, geometrie en coating. Vooral de spaanbeheersing is een actueel thema nu meer bedrijven onbemand frezen of draaien. De PKD-gereedschappen bieden hiervoor nieuwe mogelijkheden nu lasertechnologie in de bewerking van deze gereedschappen definitief doorbreekt. PKD kan namelijk niet geslepen worden, maar met behulp van de nieuwe generatie lasers slagen fabrikanten er in om spaanbrekers aan te brengen in deze harde gereedschappen.
Een nog relatief nieuwe ontwikkeling is het bewerken van bijvoorbeeld Inconel 718 met keramische wisselplaten. Kennametal heeft hiervoor een complete lijn opgezet, die onder de merknaam Sialon op de markt is. Met dit snijmateriaal haalt men snijsnelheden tot 1.000 m per minuut. De keramische snijplaten kunnen alleen ingezet worden voor het voorfrezen en semi-finishen. Het snijmateriaal vergruizelt tot stof.
Een ontwikkeling bij Iscar die in de markt goed aankomt is de wisselkopboor (foto). Tot nog toe is 12xD de maximale lengte. Iscar ziet deze Sumocham wisselboorkoppen onder andere toegepast worden voor diepgatboren op bewerkingscentra. Vanwege de dubbele snijplaten waarmee de kop is uitgerust, verbetert de productiviteit sterk.
Thermisch gedrag
Een van de grote uitdagingen voor de machinebouwers was jarenlang het thermisch gedrag van de machine. Naarmate meer en meer bedrijven overstappen op 24/7 verspanen, moet de machine thermisch stabiel zijn om ook ‘s nachts verzekerd te zijn van producten die binnen de specs vallen. Thermische fouten zijn namelijk in een groot aantal gevallen (driekwart volgens onderzoek door Makino) de oorzaak van maatonnauwkeurigheid.
Nu premium machinemerken zoals Makino, Okuma en Yasda qua constructie veel verbeteringen hebben gerealiseerd, gaat men het in andere richtingen zoeken. Dan kan het gebruik van andere materialen zijn, zoals carbon voor het bouwen van de ram. Dit levert naast goede thermische eigenschappen een gewichtsbesparing op die ten goede komt aan de dynamiek. De kleine Duitse speler Roschiwal bouwt bijvoorbeeld al samen met carbonspecialist SGL sledes van koolstofvezels, die minder dan de helft wegen van een traditionele slede. Ook het Japanse Sodick gebruikt dit materiaal, bijvoorbeeld in de tafel van een compacte freesmachine die met name op de Amerikaanse markt wordt verkocht.
Emuge-Francken en Hainbuch gebruiken carbon om klauwplaten lichter te construeren. De grote klauwplaat van Emuge- Francken (foto) bestaat deels uit staal, deels uit carbon. Het totale gewicht daalt van 460 naar 130 kilogram, wat het dynamisch gedrag van machine verbeterd. Ook het terugdringen van het energieverbruik speelt een rol bij deze ontwikkeling. De komst van sensoren en de toename van de rekenkracht van computers biedt nog een andere oplossing: compensatie voor de thermisch veroorzaakte afwijking. SHW Werkzeugmaschinen, fabrikant van grote freesmachines, ontwikkelt zo’n systeem samen met het Fraunhofer. Zeer nauwkeurige sensoren meten de vervorming van de machine en een compensatiemodel past de positie van het gereedschap aan, zodat de maatafwijking praktisch tot nul wordt gereduceerd. De Duitse machinebouwer zegt dat dit systeem een fractie kost van een laserinterferometer met een vergelijkbaar resultaat.
Geautomatiseerd programmeren
Heruit blijkt de toename van het belang van software. Dat begint al bij de CAM-programma’s. Steeds meer CAM-programma’s bevatten speciale freescycli die enerzijds voor een korter programma zorgen, anderzijds voor een meer constante belasting van de frees en dus van de machine. Veelal zijn voorfrees strategieën zoals iMachining (SolidCAM), Vortex (Delcam PowerMill) en Waveform (EdgeCam) gebaseerd op trochoïdaal frezen, waarbij het materiaal als het ware weggeschild wordt. Deze strategieën houden de frees zoveel mogelijk in het materiaal en voorkomen luchtfrezen omdat de frees van het ene gebied naar het andere moet bewegen. Het resultaat is niet alleen meer spaanvolume in dezelfde tijdspanne, maar vooral een gelijkmatige belasting van de frees waardoor de standtijd hiervan toeneemt. CAM-programmeren wint terrein.
Op de Hannover Messe liet onder andere SAP zien dat voor een aantal producten het programmeren in de toekomst nog verder geautomatiseerd zal gaan verlopen. Nu al verloopt het CAM-programmeren dankzij zaken als featureherkenning grotendeels geautomatiseerd, dat wordt volgens SAP nog meer zodra het totale productieproces wordt aangestuurd op basis van data uit het ERP-systeem van het Duitse bedrijf. Dit is in feite dezelfde richting die Bram de Koning van Cellro onlangs nog schetste tijdens de Demoweek Ede-Veenendaal. Volgens hem gaat de verspaner straks vooral de strategie kiezen waarna software automatisch de verdere werkvoorbereiding uitvoert.
Machinebesturing
De besturing op de machines wordt eveneens steeds geavanceerder. De trend hier lijkt onder andere de toepassing van apps, iets dat twee jaar geleden in gang is gezet door DMG Mori Seiki en inmiddels navolging vindt onder andere bij Okuma en Chiron. Het idee hierachter is tweeërlei. Allereerst willen de machinebouwers de weg vrij maken voor smart industry achtige toepassingen. Via apps kunnen relatief eenvoudig nieuwe functies in de besturing worden geïntegreerd, zoals OEE-metingen. Ten tweede zeggen de machinebouwers met apps en touchscreens te willen aansluiten bij de manier waarop de jongere generaties apparaten bedient.
Onderhuids zie je merkspecifieke besturingen opschuiven richting CAM-programma’s. Heel goed is dat te zien bij Mazak Smooth (foto), de nieuwste versie van de Mazatrol besturing. Hierin zitten niet alleen meer mogelijkheden om veel gebruikte parametersettings als een soort macro op te slaan, de besturing geeft bijvoorbeeld ook op basis van de effectieve inzet van de machine per as een onderhoudsadvies aan. Intelligent Mazak Check is een functie waarmee de operator softwarematig kan compenseren als de spil niet loodrecht op de tafel staat. Mazak kiest er verder voor om de besturing ook als een PC-versie aan te bieden. Deze is gekoppeld aan de machines, zodat de programmeur vanaf afstand de machines kan volgen. Eigenlijk biedt Mazak hiermee een eigen CAM-pakket aan.
Adaptieve verspaning
De toekomst van verspanen gaat, aldus sommige experts, richting adaptief bewerken. Zowel machinebouwers, CAM-ontwikkelaars als gereedschapfabrikanten praten al over de machine die zichzelf instelt, op basis van de data die uit metingen komen. Starrag zet hier stappen in samen met onder andere Renishaw. Met de Renishaw Sprint taster wordt de exacte positie van het gereedschap bepaalt waarna het virtueel – in het programma – zodanig wordt gepositioneerd dat de overmaat binnen vooraf ingegeven grenzen valt. Door de virtuele uitlijning van het werkstuk hoeft dat fysiek minder exact opgespannen te worden. Een andere toepassing is het bewerken van bijvoorbeeld giet- en smeedstukken, die niet altijd exact dezelfde maten hebben.