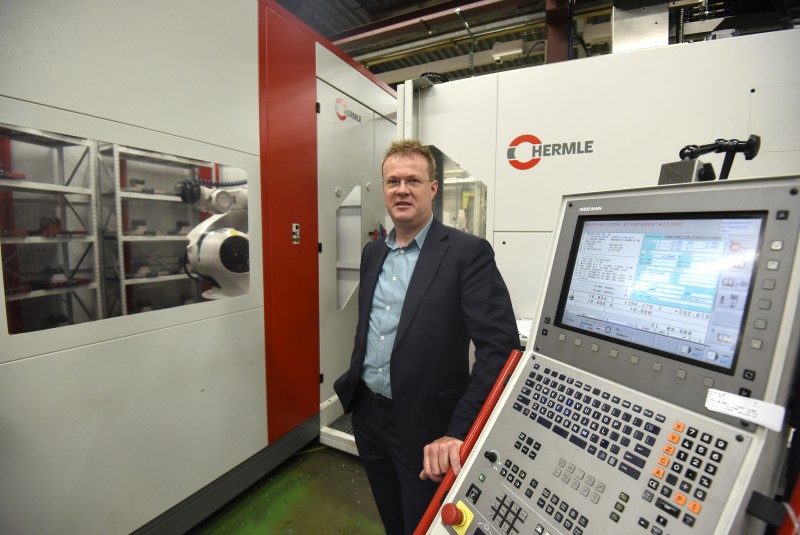
Robotisering en digitalisering veranderen verspaningsspecialist Schut PrecisionParts uit Alblasserdam langzaam in een volledig 24-uurs bedrijf. Het bedrijf haalt er werk mee binnen dat een paar jaar geleden nog naar elders verdween. ‘We zijn de komende jaren klaar voor de concurrentieslag.’
Computers en randapparatuur staan in dozen klaar voor afvoer naar de schroothoop. Schut brengt de volledige ERP-omgeving ‘de cloud in’. ‘Onze beveiligde lokale CAM-stations en het machinepark kunnen straks draadloos putten uit dezelfde bron. En we krijgen een DMS-systeem dat alles documenteert’, zegt commercieel directeur Wim van Asperen. ‘Net weer wat efficiënter dus.’ Het is een kleine stap voor het huidige bedrijf, maar een gigantische sprong gezien de geschiedenis.
Barendrecht
Het begon 68 jaar geleden allemaal met een draai- en freesbankje in de schuur van grootvader Schut in Barendrecht. Hij fabriceerde er (reparatie)onderdelen voor lokale bedrijven, vooral de Sliedrechtse baggerindustrie. Het bedrijf verplaatste naar Alblasserdam in 1963. Onder het bewind van zoons Dirk en Joop deden in de jaren tachtig en negentig de eerste machines met digitale aflezing hun intrede, gevolgd door de eerste cnc-machines. Automatisering en robotisering zijn de sleutelwoorden onder de huidige tweekoppige directie, met daarin vertegenwoordiger van de derde generatie Maurice Schut.
Achtbaan
De overstap van puur mechanisch naar computergestuurd betekende een overgang naar het gespecialiseerde fijnmechanische werk. Terwijl een conventionele machine tot pakweg een tiende millimeter nauwkeurig kan werken, haalt een cnc-gestuurde machine toleranties tot een paar micron. ‘Zowel proto’s als enkelstuks bestellingen passen prima in het proces van verdere flexibilisering’, vertelt Van Asperen. Programmeren en instellen van machines en gereedschappen kost tijd, maar die is het dubbel en dwars waard. Schut PrecisionParts haalt voldoende en interessant werk uit onder meer de attractie- en de railindustrie. Veel wagentjes die over de achtbanen in de Nederlandse attractieparken denderen zijn samengesteld uit in Alblasserdam verspaande onderdelen. Daarnaast produceert het bedrijf sinds begin jaren tachtig wielbanden en aandrijfassen voor voertuigen van verschillende vervoersbedrijven in de nationale en internationale railindustrie. Recentelijk sleepte Schut in deze sector nog een Europese tender binnen voor zo’n 2,5 miljoen euro.
Halffabricaten
Hoogwaardig staal voor chassisonderdelen komt als grote blokken (‘hondenbotten’) binnen bij de productiehal. Deze halffabricaten wegen ongeveer negenhonderd kilo, maar er zijn ook grotere en zwaardere exemplaren. Soms is een onderdeel van twee meter nodig uit massief staal. Het is een kwestie van ervaring hoe je een dergelijk klus aanpakt. Van Asperen: ‘Moet je eerst voorbewerken of kun je meteen doorgaan met frezen? Verkeerd voorbewerken en te snel verspanen heeft als resultaat dat het werkstuk krom trekt. Een goede voorbewerking is nodig om de spanning gelijkmatig over het materiaal te verspreiden.’
Gietblokken
Veel opdrachten zijn bestemd voor de Nederlandse markt maar er gaat ook het nodige naar Duitse machinebouwers. Recentelijk nog kwam een grote order van een half miljoen euro binnen voor onderdelen voor een Duitse specialist in magneetsystemen. De nabijgelegen petrochemische industrie van Rotterdam en Moerdijk is een grootafnemer van op maat gemaakte kleppen en afsluiters.
Een voorbeeld van een zeer specialistische klus is een recent geproduceerde serie gietblokken (500 x 120 millimeter) voor een aluminiumproducent. Verschillende concurrenten beten zich de tanden er op stuk, want een blok van dergelijke omvang trekt bij bewerking en harding al gauw krom. Schut wist ze met een zeer hoge nauwkeurigheid te leveren.
Het bedrijf uit Alblasserdam produceerde ook de onderdelen voor aandrijving van de racewagens van het Dutch Racing Team en de fundatiebrackets voor het Hyperloop project van de TU Delft. Een uitdaging waren ook de ‘inconel’ cilinders van de Maeslantkering. ‘Het geeft toch een kick dat je machines zoiets aankunnen’, zegt Van Asperen. ‘Bij zulke opdrachten in dit materiaal en in het µ-bereik moeten veel producenten afhaken.’
Om aan de voortdurend fluctuerende vraag te kunnen voldoen beschikt het bedrijf over een machinepark met zestien cnc-gestuurde verspaningsmachines waarvan er drie voorzien zijn van robotisering. Een meetruimte met uiteenlopende meetinstrumenten, waaronder een 3D-cnc-meetmachine, onderstreept waarvoor het bedrijf staat: precisie. In vaste dienst zijn ‘slechts’ achttien man personeel, maar de arbeidsproductiviteit is groot dankzij de automatisering.
Robotarm
Paradepaardje van het bedrijf zijn twee robotcellen. De grootste ervan kan zelfstandig opgespannen werkstukken tot 250 kilo in en uit een vijfassige Hermle verspaningsmachine nemen. Er zijn dertig palletplaatsen beschikbaar waardoor deze productiecel volcontinu aan dertig verschillende producten kan werken. Hiermee produceert deze geoptimaliseerde productiecel gemiddeld 22 uur per dag.
Het kleinere exemplaar, dat stug doordraait in het hart van de fabriek, is gekoppeld aan een draai-freescombinatie en een freesbank. Als de draai-freescombinatie klaar is met een bewerking, neemt de robotarm het product uit, blaast het schoon en plaatst het eventueel in de freesbank voor verdere bewerking. De productiecellen beschikken over productiebewaking ten behoeve van proceswaarborging. Momenteel wordt gewerkt aan een optimalisering voor het volautomatisch afbramen. Op die manier moet het werk in de fabriek steeds meer richting een volcontinu proces verschuiven. ‘Robotica zorgt voor enorme flexibilisering en capaciteitsvergroting, waardoor we het totaalproces beter kunnen optimaliseren’, vertelt Van Asperen. ‘We trekken veel meer werk binnen dankzij onze robots.’
Er wordt ook werk teruggehaald dat de afgelopen tien jaar naar lagelonenlanden verdween. Dankzij flexibele automatisering en het vermogen om volcontinu te werken is fijnmechanische verspaning haalbaar tegen concurrerende prijzen. Het lukt bovendien om dat te doen met een constante kwaliteit.
Klinkt alsof het toptijden zijn, maar zo ver wil Van Asperen niet gaan. De naweeën van de crisis zijn wel degelijk voelbaar. De prijzen staan nog onder druk, prijsvechters doen alles om een opdracht binnen te halen. De remedie daartegen is nóg efficiënter werken. Overbrenging naar de cloud van de erp-omgeving is daarvan een voorbeeld.
Serieuzer reden tot zorg is het vinden van gekwalificeerd personeel. Van Asperen: ‘Waar haal je goede verspaanders vandaan? Er worden er veel te weinig opgeleid.’ Via leerwerktrajecten probeert Schut als erkend leerbedrijf toch aan voldoende aanwas te komen.
Binnenkort hoopt Schut zijn AS9100-certificering binnen te halen, bovenop de bestaande ISO-certificeringen van 9001 en 14001. Een intensief traject, maar het bedrijf kan dan ook voor de luchtvaartsector gaan werken.