Auto’s lichter maken, levert voordelen op in brandstofverbruik met als gevolg minder CO2-uitstoot. En omdat auto’s in zulke enorm grote hoeveelheden worden geproduceerd, is de impact van zelfs kleine gewichtsbesparende maatregelen per saldo heel groot.
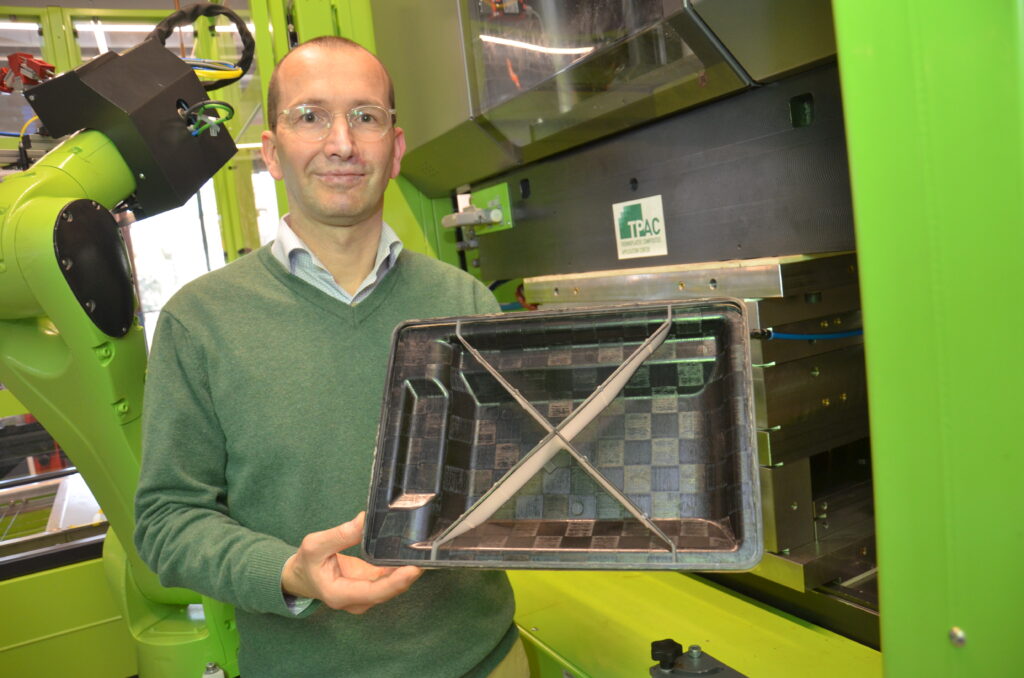
Het onderzoekscentrum voor toepassingen van thermoplastisch composiet TPAC van Saxion Hogeschool in Enschede werkt met partners in een Europees project aan het vervangen van stalen auto-onderdelen door een veel lichter en bovendien recycleerbaar composietmateriaal, op een manier die past in de maakprocessen van de bestaande kunststofverwerkende industrie. Directeur Ferrie van Hattum van TPAC werkt samen met het bedrijfsleven en met verschillende universiteiten aan circulaire oplossingen voor de auto-industrie. ‘Het doel is met lichtgewicht onderdelen het staal in auto’s te vervangen daar waar dat kan. In ons zogenoemde 3D FAIM-project werken we met het bedrijfsleven en de universiteiten aan slimme én circulaire oplossingen voor de auto-industrie. We laten op Europees niveau zien dat nieuwe technologieën op een industriële schaal in de automotive sector kunnen worden toegepast’, aldus Van Hattum. ‘Hier in Nederland hebben we van oudsher natuurlijk niet een grote auto-industrie. Maar in Duitsland is die er wel en vandaar dat wij voor ons 3D FAIM-project op Europees niveau onderzoek doen naar het ontwikkelen en produceren van lichtgewicht onderdelen die op een veilige manier staal kunnen vervangen, bijvoorbeeld in auto’s.’
Fiber Application & Injection Moulding
Saxion TPAC ging in 2018 met technische universiteiten uit Duitsland, Polen en Italië en met een groot aantal Europese bedrijven van start met dit onderzoeksproject met de naam 3D-FAIM waarin alles draait om Fiber Application & Injection Molding: dit is het maken van onderdelen voor auto’s uit composiet, waarbij het maakproces ook nog eens is in te passen in de huidige kunststofverwerkende industrie. ‘Het beste van beide werelden dus, met als doel op een efficiënte manier lichtere onderdelen voor auto’s te produceren. Onderdelen die aan het einde van de levenscyclus ook nog eens kunnen worden hergebruikt. ‘Per auto levert elke kilo gewichtsbesparing over de gehele life cycle pakweg zeven liter brandstofbesparing op. En omdat je bij auto’s al gauw praat over onderdelen die tien tot twintig kilo wegen, zet dat dus snel zoden aan de dijk’, berekent Van Hattum. ‘Winst is bijvoorbeeld te behalen in een autostoel. Van oudsher heeft die een stalen frame, wat een relatief zwaar onderdeel is. De keuze voor het stijve en veilige staal werd oorspronkelijk niet voor niets gemaakt, maar dankzij een nieuwe toepassing zoals composiet is er een lichter alternatief mogelijk dat diezelfde, onwrikbare eigenschappen in zich draagt. Het is best pittig met een stuk staal te concurreren want daarin zit zestig jaar optimalisatie. Maar composiet stelt ons in staat het maakproces van zo’n frame heel anders vorm te geven.’
Minus dertig procent
Volgens Van Hattum komen uiteindelijk veel semi-structurele onderdelen van een auto in aanmerking om op een nieuwe manier van lichter materiaal te worden geproduceerd. Dat kan leiden tot auto’s die zo’n dertig procent minder wegen, met dezelfde eigenschappen qua veiligheid. ‘Of neem elektrische auto’s, die kunnen straks met kleinere batterijen worden uitgerust want met minder gewicht kom je een stuk verder.’
Maar er is meer mogelijk. TPAC ging met de partners en de studenten een stap verder. ‘Wij proberen de composiettechnologie zo te ontwikkelen dat we die inpassen in de maakprocessen van de bestaande kunststofverwerkende industrie. Dashboards en schaaldelen voor auto’s worden al van kunststof gemaakt. Maar omdat kunststof niet voor alle onderdelen van de auto sterk genoeg is, moeten ze vaak nog op een stalen deel worden bevestigd.’ Wanneer dat deel door composiet wordt vervangen, vormen beide materialen samen een sterk, maar licht alternatief voor de auto-onderdelen, aldus Van Hattum. ‘We hebben daarvoor een 3D-printproces ontwikkeld waarmee we een insert van composiet, een soort geraamte, kunnen maken dat precies op die plekken neergelegd wordt waar we de sterkte en stijfheid van het materiaal nodig hebben. Wanneer we dat deel vervolgens overspuiten met kunststof, hebben we óók het dashboard of het stoelframe dat we willen hebben, maar dan vele malen lichter.’
Over vijf jaar
In de huidige generatie auto’s wordt al volop met lichter materiaal gewerkt. Het onderzoek van TPAC en de partners richt zich vooral op de volgende generatie voertuigen die over een jaar of vijf profiteert van de nieuwe technologische toepassingen. ‘We gaan vanuit onze expertise niet het mobiliteitsprobleem oplossen maar we zorgen er wel voor dat voortbewegen van de auto energie-efficiënter kan door een lager gewicht. Bovendien kan je thermoplastische kunststoffen van dit type hergebruiken. Aan het einde van de rit demonteer je de auto, gooi je het kunststofmateriaal in de shredder en pers je er nieuwe producten van die weer opnieuw in een auto gebruikt kunnen worden.’
Portier demonstrator
Hoewel er in de afgelopen jaren intensief kon worden samengewerkt tussen het TPAC-lab in Enschede en het lab van de Technische Universiteit van Chemnitz in Duitsland, liep de laatste fase van het onderzoeksproject door corona-restricties wat vertraging op. ‘We werken met de Technische Universiteit Chemnitz daarom nu nog aan een demonstrator van een autoportier. Met dat project gaan we aantonen dat we met de inzet van composiet in kunststof in een spuitgietproces een impactbalk van een autoportier kunnen maken, waarbij we dus ook het traditioneel uit staal geproduceerde deel vervangen door kunststofcomposiet. Dit wordt de volgende stap in ons onderzoek dat laat zien dat we in een Europees samenwerkingsverband onze nieuwe technologieën op industriële schaal in de automotive sector kunnen toepassen.’