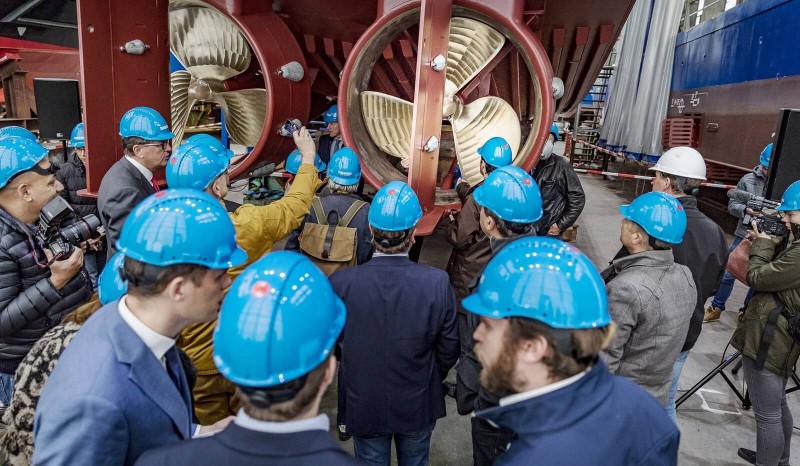
NLR heeft onlangs een metalen compressorwiel van een microturbine geproduceerd met 3D-printing. Dit wiel is ook nog eens succesvol getest tot 200.000 omwentelingen per minuut.
Hiermee heeft NLR een eerste stap gezet richting het 3D-printen van roterende componenten. Het 3D-printen van roterende componenten vormt een uitdaging omdat deze componenten tijdens gebruik kritisch belast worden.
Titaanlegering
NLR heeft een bestaand compressorwiel opgemeten met een 3D optische scanner en vervolgens met speciale software herontworpen. Het herontwerp was gericht op printbaarheid en gewichtsreductie en niet op een aerodynamische verbetering. Tijdens het herontwerp zijn de spanningsniveaus als gevolg van de gewichtsreductie doorgerekend voor de gebruikscondities.
Het herontwerp is geprint in een titaan legering. Na warmtebehandeling, mechanische nabewerking en balancering is het geprinte compressorwiel getest in de bij NLR aanwezige microturbine testopstelling bij een toerental van 200.000 omwentelingen per minuut en een temperatuur van ongeveer 150°C. De systeemprestaties van het 3D-geprinte compressorwiel bleken vergelijkbaar met die van het origineel. Hiermee heeft NLR bruikbare kennis opgedaan met het herontwerpen van een bestaand roterend onderdeel en het 3D printen hiervan.
Met het 3D-geprinte compressorwiel heeft NLR een nieuwe stap gezet op het gebied van additieve productie. Nadat eind 2016 een statisch belast onderdeel voor de NH-90 helikopter is geproduceerd, is nu een volgende stap gezet door 3D-printing toe te passen voor een roterend en kritisch belast onderdeel. De 3D-scanning en printing capability van NLR is geconcentreerd in het Metal Additive Manufacturing Technology Centre- MAMTeC van NLR in Marknesse. Dit centrum beschikt naast een poederbedmachine over test- en modelleercapaciteit en is daarmee hét onderzoekscentrum voor het 3D-printen van metalen in Nederland.
Beter dan traditioneel
Met behulp van 3D-printen kunnen vliegtuigonderdelen sneller vervaardigd worden en kan er op onderhoudskosten bespaard worden. Daarnaast kan 3D-printen een bijdrage leveren aan gewichtsreductie van vliegtuigen, waardoor vliegtuigmaatschappijen hun brandstofverbruik en daarmee schadelijke emissies kunnen reduceren.
Er komen steeds meer voorbeelden van geslaagde 3D-metaalprints. Zo is in de eerste week van dit jaar is ‘s werelds eerste 3D-geprinte offshore kraanhaak geslaagd voor de overbelastingstest (80mt) en alle bijbehorende kwaliteitscontroles. Waar kraanhaken meestal worden vervaardigd met giet- of smeedtechnieken, gebruikt Huisman Waam voor de productie van middelgrote tot grote componenten van hogesterkte staal, waaronder een grote viertandshaak met een geprint eigen gewicht van 1000kg. Dit leidt tot kortere levertijden tegen een concurrerende kostprijs en volgens Huisman zelfs een consistenter kwaliteitsniveau.
De productiemethode stelt het bedrijf bovendien in staat om componenten met complexe vormen, korte levertijden of lokaal alternatieve materiaaleigenschappen te leveren, die eerder fysiek onmogelijk of commercieel onhaalbaar waren.
Scheepsschroef
En eind vorig jaar haalde Damen Shipyards alle kwaliteitscertificaten voor zijn 3D-geprinte scheepsschroef, de zogeheten Waampeller. Waam staat hier voor Wire Arc Additive Manufacturing, een manier van 3D-printen die lijkt op het oplassen van vele lagen nikkelaluminiumbronslegering tot een scheepsschroef.
De 400 kilo zware schroef met een diameter van 1,30 m werd vervaardigd in samenwerking met het Rotterdam Additive Manufacturing Lab (Ramlab ) en vertoonde in alle tests hetzelfde gedrag als een gegoten propeller. Het testprogramma omvatte naast de snelheidsproeven ook trekplug- en crashstop-testen.