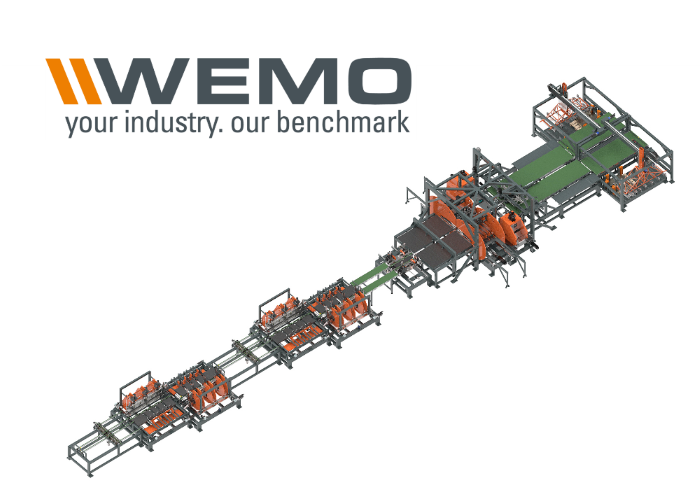
Wemo rondt binnenkort de grootste order uit de geschiedenis van de Brabantse machinebouwer af. Voor een Duitse producent van schakelkasten legt Wemo de laatste hand aan twee volautomatische productielijnen. Deze komen in Duitsland in een compleet nieuwe fabriek van de toekomst te staan. Hierin worden de schakelkasten geautomatiseerd in seriegrootte 1 gemaakt, op bestelling van de eindklant.
Twee lijnen die elk 10 miljoen euro per stuk kosten. Voor een machinebouwer die doorgaans een omzet boekt tussen de 20 en 25 miljoen euro, is dat mega. ‘De grootste order uit onze geschiedenis’, zo zei Werner van der Burgt, marketingcoördinator, het bij een presentatie aan een handvol VIP klanten. Nu de productie van de beide lijnen in de afrondende fase zit, kregen zij de kans om met eigen ogen te zien wat mogelijk is op het vlak van geautomatiseerd plaatbewerken.
Zes jaar
De order kent een lange voorgeschiedenis. Al in 2012 heeft de Duitse klant, marktleider in Europa als het om productie van schakelkasten voor de machinebouw gaat, de eerste keer met de Nederlandse machinebouwer gesproken. Dat was precies een jaar nadat in Duitsland de term industrie 4.0 was gelanceerd. ‘Ze wilden een nieuwe fabriek bouwen, maar hadden nog geen beeld van de technologie die echt nodig is. Wel dat ze zowel seriegrootte 1 als batches wilden produceren, omsteltijden nul, automatisch beladen, aansturen vanuit het ERP-systeem en flexibel om later ook andere producten te kunnen maken’, vat Hans Flipse van Wemo de uitdaging samen. Uiteindelijk is in de zomer van 2015 de opdracht gekomen voor de eerste lijn en vlak voor de zomervakantie in 2017 de opdracht voor de tweede lijn.
CNC-gestuurd
De beide lijnen worden straks beladen door AGV’s, die orders krijgen vanuit het ERP-systeem. Wemo slaagt er vervolgens in om het hele proces van ponsen, lassen en buigen manloos te laten verlopen. In batches van 1 stuks, waarbij er 250 verschillende producten op één lijn geproduceerd kunnen worden. Het ERP-systeem zorgt voor de aansturing, op basis van de orders die de klanten via het webportal plaatsen. Voor het lassen gebruikt men de lastechnologie van AWL. Het hart van de technologie die Wemo in de lijn integreert, is de servogestuurde CNC-buigtechnologie. Vier van dergelijke units zitten er in de eerste productielijn. ‘Terwijl één product wordt gebogen, stelt de buigmachine de gereedschappen al in voor het volgende product. Omsteltijden zijn dus nul’, aldus Werner van der Burgt. Cyclustijd op de eerste lijn bedraagt 25 seconden, die op de tweede 11 seconden. Omdat de Wemomachine het hart is van de schakelkastenproductie, wil de opdrachtgever niet het risico lopen dat de hele fabriek stil komt te liggen door een storing in de Wemo-lijn. ‘Daarom hebben we de CNC-buigunits redundant uitgevoerd met een keerstation. Bij een eventuele storing kunnen de plaatdelen gedraaid worden zodat alle vier de kanten door één unit gebogen kunnen worden.’
Augmented reality
De machines van Wemo passen helemaal in het industrie 4.0-concept dat de Duitse kastenbouwer in de nieuwe fabriek gaat realiseren. Om de operator die vooral bezig is met onderhoud en het optimaliseren van de productielijn te ondersteunen, zet Wemo augmented reality in. De operator ziet met een Microsoft Hololens allerlei belangrijke informatie van het station waaraan hij werkt. Ook kunnen de experts vanuit Den Bosch meekijken en ondersteuning bieden. Werner van der Burgt: ‘De operator krijgt andere taken, net als technische diensten die veel meer bezig zijn met procesanalyse hoe ze de lijn kunnen verbeteren. Omdat onze technologie steeds complexer wordt, proberen we dit te vereenvoudigen met AR-toepassingen.’
De beide productielijnen gaan eind juni naar de Duitse klant. Wemo heeft ze zo gebouwd dat ze binnen een week operationeel kunnen zijn.