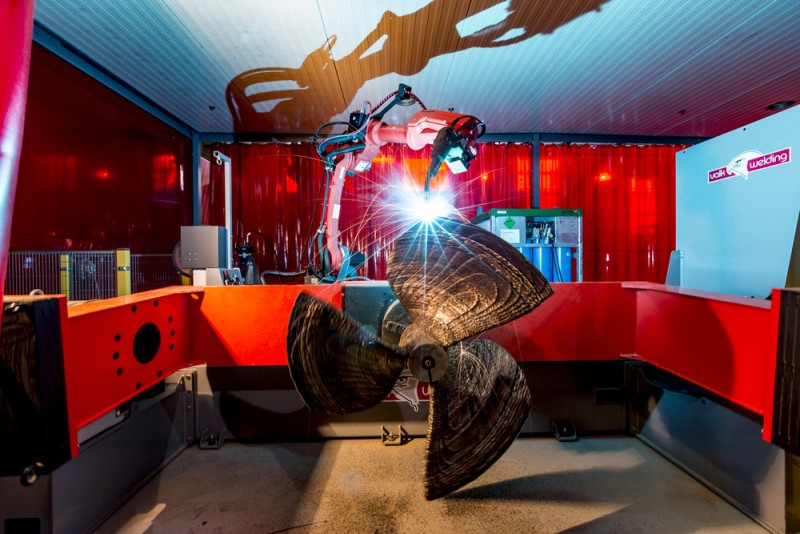
3D-metaalprinten is al lang niet meer het exclusieve domein van de poederbedmachines, waarbij een laserstraal metaalpoeders aan elkaar smelt. Direct Energy Deposition (DED) ontwikkelt zich zeker zo snel, misschien wel sneller. De grote troef van deze 3D-metaalprinttechnologie: hybride producten. De combinatie van 3D-metaalprinten en klassieke metaalbewerkingstechnieken.
Lasercladden bestaat al lang. De laatste tijd is daar de 3D-variant bijgekomen, waarbij met een laser, een gas en een metaalpoeder ook 3D-onderdelen kunnen worden opgebouwd. In de officiële terminologie zoals deze tegenwoordig geldt, noemt men deze techniek Direct Energy Deposition (overigens niet alleen met poeder). DMG Mori is al een flink aantal jaren actief met deze technologie met de Lasertec 65 3D, een hybridemachine. Echter vooral het aantal toepassingen waarbij DED-technologie als standalone techniek wordt ingezet, groeit. Het Fraunhofer ILT wijde er eerder voorafgaand aan het lasercongres AKL dit jaar zelfs een hele studiedag aan.
Hybride werkstukken
En niet zonder reden: de mogelijkheden van deze printtechnologie zijn groot, enerzijds omdat je hiermee grote werkstukken kunt maken, anderzijds omdat de technologie zich leent voor hybride werkstukken. Dit zijn werkstukken die deels gemaakt zijn met conventionele technologie zoals CNC draaien of frezen, en deels met 3D-metaalprinten. Of gieten en daarna printen. ‘Als we basis gietstukken kunnen aanpassen met 3D-printen, kunnen we kosten en levertijden besparen’, aldus Jan Bremer, een van de onderzoekers van het Fraunhofer ILT.
Trumpf, een van de grotere spelers op dit vlak, liet op een van de beurzen en op de eigen huisshow een goed voorbeeld hiervan zien. Een fijngiet-werkstuk is lokaal verstevigd met ribben die met 3D-metaalprinten zijn aangebracht. In Aken wordt een dergelijke toepassing onder andere samen met autobouwer Ford onderzocht. Het idee hierachter is dat men een basisproduct zonder extra gereedschappen kan aanpassen aan de gewijzigde eisen die een productvariant stelt.
Ook Mercedes-Benz onderzoekt de mogelijkheden van deze technologie, maar dan voor het repareren van dure persgereedschappen. Ook het aanpassen van gereedschappen voor kleinere series wordt onderzocht. Het zou de autofabrikant tot 10 procent van de gereedschapskosten besparen. Een bijkomend voordeel van persgereedschappen is dat men deze minder zwaar kan maken door de structuur te optimaliseren. Tobias Todzy, die bij de AM-activiteiten van Mercedes in Sindelfingen betrokken is, vindt dit een niet te onderschatten aspect van 3D-geprinte persgereedschappen. ‘Als de pers omhoog beweegt kost dit veel energie.’ Een voorbeeld is een prototype van een snijstempel waarvan het gewicht bijna is gehalveerd. In een test heeft men in Sindelfingen meer dan 600 onderdelen geperst met dit gereedschap.
Kwaliteit reproduceren
Zijn er dan geen nadelen aan dit proces? Toch wel, maar die zijn oplosbaar, lijkt het. De technologie is erg gevoelig voor porositeit. Met een andere, spiraalvormige beweging van de laser kun je dit risico minimaliseren, laten de onderzoekers in Aken zien. Goede procescontrole om consistente kwaliteit te produceren, is een ander punt waar aan wordt gewerkt. De hoeveelheid energie van de laserstraal meten kan al langer. Nu heeft het Fraunhofer ILT ook een technologie ontwikkeld om de hoeveelheid poeder die toegevoerd wordt nauwkeurig te meten, net als de richting waarin deze wordt ingevoerd. Gecombineerd met camerabeelden van elke laag die wordt geprint, kan men op deze wijze de kwaliteit aanzienlijk beter sturen en beter reproduceren. Daarmee kan met tot op 10 µm nauwkeurige geometrische vormen printen met deze technologie.
3D-printen met lasdraad
Deze 3D-metaalprinttechnologie werkt niet uitsluitend met metaalpoeder. Er zijn ook fabrikanten die kiezen voor lasdraad die gesmolten wordt. Dat gebeurt onder andere in het Rotterdamse RAMLab, waar met behulp van een robot de eerste gecertificeerde scheepsschroeven zijn geprint. De belangrijkste voordelen zijn dat lasdraad gemakkelijker te verwerken is, er een heel groot aanbod van legeringen beschikbaar is én de kosten veel lager zijn dan van poeder. Het nadeel is dat het geprint werkstuk nog grover is en dus meer verspanende nabewerking vergt. Desondanks kan het uiteindelijk goedkoper zijn.
Een fabrikant zoals Gefertec, die ook lasdraad gebruikt, kiest niet voor een robot maar voor een drie- of vijfassig bewerkingscentrum, gebouwd op basis van Siemens aandrijftechnologie. De complete technologie zit in een afgesloten machine. Het voordeel van deze keuze is dat het programmeren van de machine eigenlijk niet veel anders is dan het programmeren van een CNC-freesmachine, alleen bouwt men materiaal op in plaats van het weg te halen. De specifieke lasparameters (gebaseerd op Fronius CMT-technologie) zit in de software die op de achtergrond draait. De bewegingen van de drie of vijf assen laten zich programmeren via Sinumerik. Het Duitse bedrijf is onlangs gaan samenwerken met Getrom, een fabrikant van freesmachines gebaseerd op parallelle kinematica. Getrom integreert de 3D-metaalprinttechnologie in een mobiele CNC-machine die in vrij korte tijd bij de klant wordt opgebouwd. Toepassingen waar men aan denkt zijn onder andere reparatie van matrijzen, grote persgereedschappen en offshore producten waar bijvoorbeeld een flens aan een bestaand product moet worden aangebracht. Dat kan samen met de verspanende nabewerking in één procesgang gebeuren.
VS investeren in DED-technologie
In de VS wordt momenteel fors geïnvesteerd in de ontwikkeling van deze 3D-printtechnologie. Meerdere bedrijven begeven zich op deze markt. 3D-Hybrid ontwikkelt complete kits, inclusief printkop en software, om te integreren in bestaande CNC-machines. Een van de eerste Europese machinebouwers die voor deze oplossing kiest, is Hamuel in Duitsland. Andere Amerikaanse bedrijven bouwen specifieke machines voor deze printtechnologie, zoals DM 3D dat onder andere een gesloten machine heeft ontwikkeld voor werkstukken tot 10 ton. DM 3D zet in op hybride werkstukken. Een van de sectoren waarin het bedrijf actief is, is de olie- en gasindustrie waar men gereedschappen repareert en zowel de kosten als de doorlooptijd fors reduceert. Vooral dit laatste is in deze sector belangrijk. Optomec is een andere Amerikaanse speler die verschillende type machines ontwikkelt. De grootste beschikt over vier poederdoseerunits, zodat vier legeringen verwerkt kunnen worden, en een laserbron van 3 kW (fiberlaser). Sciaky is de derde Amerikaanse speler en kiest voor een andere benadering. Als energiebron wordt een elektronenstraal gebruikt, met als gevolg dat het proces zich in een vacuümkamer afspeelt. Dat verhoogt de kosten voor de machines aanzienlijk, maar heeft als voordeel dat de hoeveelheid materiaal die men in een uur tijd print, hoger ligt dan bij de andere DED-technieken. Sciaky kan bijvoorbeeld titanium 3D-printen met 12 kilo per uur.
3D-printen: de stand van zaken
Er wordt veel geroepen en geschreven over 3D-printen. De echte doorbraak laat echter nog op zich wachten, afgezien van sectoren zoals de luchtvaartindustrie en de medische sector waar de technologie wel zijn weg naar serieproductie begint te vinden. Deze zomer brengt Vraag & Aanbod een serie artikelen waarin zowel wordt ingegaan op de ontwikkelingen bij de verschillende technieken en materialen maar waarin ook de relatie wordt gelegd tussen smart industry en 3D-printen. Zorgt de digitalisering van de maakindustrie er uiteindelijk voor dat 3D-printen een standaard productietechnologie wordt?
In deze editie (en in de papieren editie van Vraag & Aanbod, week 28/29) dus over Direct Energy Deposition, zoals de officiële term is voor 3D-lasercladden. In deel 2 (Vraag & Aanbod, week 30/31) werd ingegaan op goedkopere alternatieven voor het klassieke poederbed proces . Deel 3 is het laatste deel en gaat over het printen met kunststof, dat in een toenemend aantal toepassingen een volwaardig alternatief voor metalen onderdelen kan opleveren.