Broshuis B.V. uit Kampen boekte eind vorig jaar een order van meer dan 500 diepladers voor het Amerikaanse leger. Deze volgde op eerdere orders voor de US Army. Niet gek dus dat de fabrikant van opleggers, met het oog op verder groei, een nieuw stuk grond in Kampen heeft aangekocht. Een lasrobotinstallatie met een opspanbreedte van 18 meter die volgend jaar wordt opgeleverd, zorgt voor verdere capaciteitsuitbreiding.
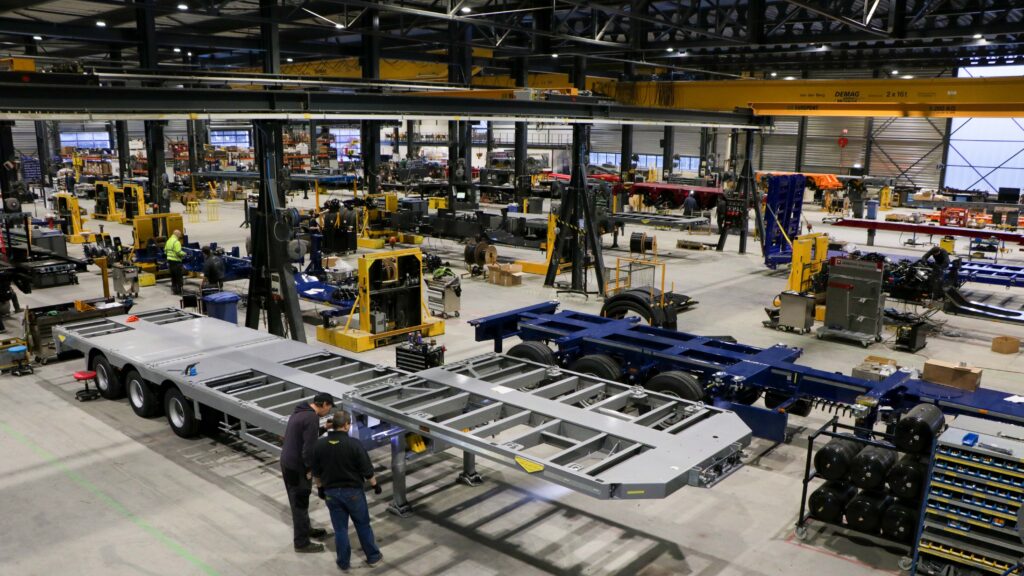
John Okken is improvement engineer bij Broshuis. Hij is verantwoordelijk voor zowel het tekenen van lasmallen als het programmeren en afstellen van de lasrobots. ‘We hebben twee kleine lasrobots, op een H-frame. En twee grotere. Ze hebben twee cellen, zodat er links gelast kan worden terwijl rechts een werkstuk wordt verwisseld en vice versa’, vertelt hij. Het mag duidelijk zijn, een significant deel van het werk bij Broshuis bestaat uit lassen. In 2023 verbruikten ze er maar liefst 100.000 kilo lasdraad in een mix van handmatig en automatisch lassen. Hoewel robots sneller en consistenter kunnen lassen, vereist robotisering in het productieproces nog veel aandacht, vooral omdat de producten die in de loop der jaren zijn ontworpen, niet altijd geschikt zijn voor de lasrobots. Om dit te optimaliseren zet het bedrijf stappen richting “design for welding,” waarbij producten specifiek worden ontworpen met robots in gedachten.
Doelstelling
In de komende vijf jaar streeft Broshuis naar 80% robotisering, een ambitieuze doelstelling. Maar noodzakelijk, want één van de grootste uitdagingen voor het bedrijf is het tekort aan vakmensen. Vakmanschap, hoewel belangrijk, wordt steeds schaarser. Broshuis heeft op dit moment veel ervaren vaklieden die exact weten hoe trailers gelast moeten worden. Maar om te anticiperen op toekomstige tekorten wil het bedrijf de intelligentie van hun engineeringsmodellen vergroten. Daardoor kunnen robots steeds meer laswerk overnemen en dat biedt wel voordelen. Robots leveren een consistente kwaliteit, zijn niet gevoelig voor menselijke factoren en ze kunnen veel uren maken zonder onderbreking. Ondanks de voordelen van robotisering zal er altijd een rol blijven voor vakmanschap. De expertise van ervaren lassers blijft nodig om de processen te optimaliseren. Maar de robots vergroten de veiligheid van het productieproces. Grote producten die handmatig gelast moeten worden, vereisen veel handelingen zoals draaien en positioneren, wat met een robot veiliger en efficiënter gaat.
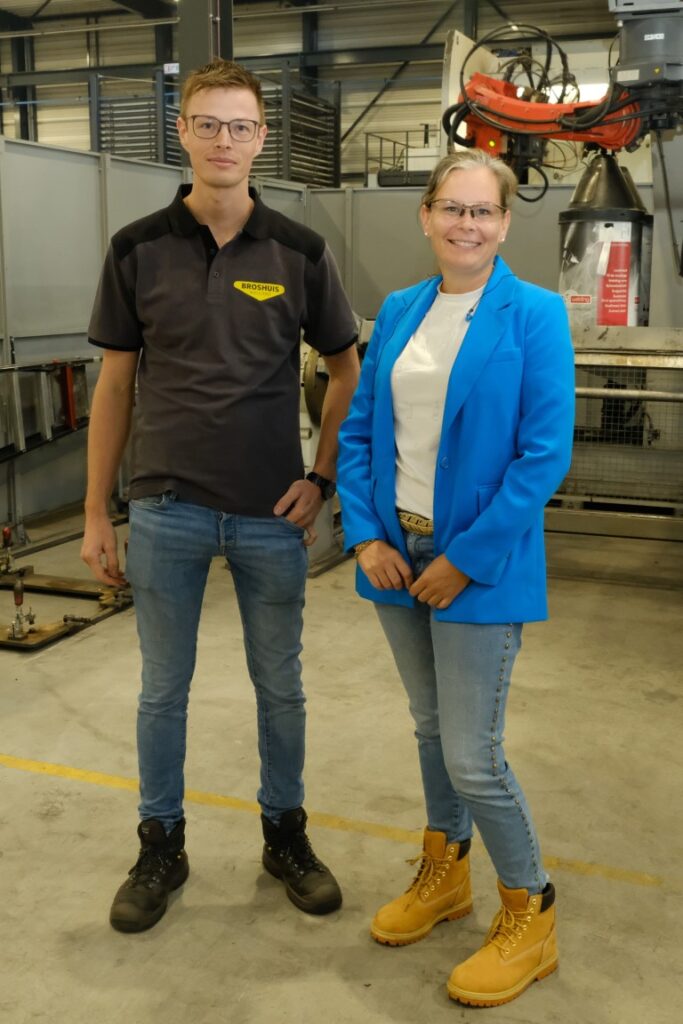
Naast ruim honderd lassers in dienst, maakt Broshuis momenteel gebruik van vier lasrobots. En nummer vijf en zes, als je telt per lastoorts, komen eraan. Zoals gezegd is de volgende lasrobot al besteld. ‘Op onze huidige robots kunnen we producten tot maximaal 3,5 meter lassen. De nieuwe, grote installatie heeft twee lastoortsen en 18 meter tussen de manipulatoren. En die zijn ook zwaar genoeg om een hele trailer in op te spannen’, illustreert Okken het verschil. Dat betekent dat bepaalde werkstukken die voorheen alleen met handlassers gelast konden worden, nu ook automatisch gelast kunnen worden. Maar daar zit nog wel wat werk in verwacht operationeel directeur Melanie Van Beek. ‘We hebben hier producten waarbij nog niet is nagedacht of er wel een lasrobotarm tussen past. Dat design for welding wordt de komende jaren heel belangrijk’, weet ze. Het idee is om de robot te plaatsen en de eerste producten op te spannen om te kijken waar ze tegenaan lopen. ‘Ja, we kunnen niet meteen 100% aflassen. Maar we laten de engineers zelf kijken waarom het soms niet lukt. Misschien dat als ze ergens een vleugel verplaatsen, of een hap uitnemen, het ineens wel lukt. Daar moeten we naar op zoek.’
Warmte
Een ander aandachtspunt is het verschil in warmte-inbreng van een lasrobot ten opzichte van handlassers. Normaal gesproken zitten er twee lassers op één hele wagen en die zijn soms wel drie weken aan het lassen. ‘Dan heb je veel meer verspreiding van warmte-inbreng. Een lasrobot wordt niet moe en kan 24 uur per dag lassen’, legt Van Beek uit. ‘Dan breng je veel meer hitte in. Waar gaat dat staal zich naartoe bewegen?’ Okken vult aan: ‘Dat kun je niet voorspellen. Want dat ligt ook aan je staalplaat. Hoe is deze gewalst, gesneden. Hoe is deze nabehandeld. Dat beïnvloedt het proces allemaal.’
Testperiode
De robotinstallatie, die rond april wordt opgeleverd, gaat daarom eerst een testperiode in. Vanaf december 2025 zal hij productie kunnen draaien op een prettig tempo. Omdat de robot offline is te programmeren, is er nu al een digitaal model beschikbaar voor een demonstratie. Okken laat zien hoe de manipulator het werkstuk kan draaien, en omhoog en omlaag kan brengen. Daaromheen bewegen twee robotarmen met lastoortsen zodat vrijwel elke laspositie bereikt kan worden. Een camera volgt de lasnaad en stuurt bij waar nodig. ‘Je hebt altijd te maken met bouwspeling’, legt Van Beek uit. ‘Het is goed om te programmeren waar wat zit, maar als je met sensoren en camera’s de lasnaad precies kan volgen, heb je veel minder afkeur en problemen.’
Snijden
Broshuis snijdt materiaal tot 20 mm dikte en 3 m x 1,5 m zelf. Het dikkere snijwerk, en het draai- een freeswerk besteedt de trailerbouwer uit. Maar alle samenstellingen die op de grote lasrobot aan elkaar worden gelast, zijn daarvoor elders in de fabriek door lassers of de kleinere lasrobots in elkaar gelast. Sommige samenstellingen, van speciale staalsoorten, moeten eerst gecontroleerd op temperatuur worden gebracht. Daarna worden ze op de middelgrote lasrobot gelast en daarna worden ze gecontroleerd weer afgekoeld, waarna ze naar de grote lasrobot kunnen voor de volgende lasbewerking. De nieuwe lasrobot wordt in hal 7 geplaatst, waar ook de andere lasrobots staan. Door alle lasrobots gecentreerd in één hal te hebben, kunnen ze beter worden beheerd en onderhouden.
Tijdswinst
Hoeveel laswerk, en -tijd er in een oplegger gaat zitten, hangt natuurlijk helemaal samen met het type oplegger. ‘Toen wij begonnen met de achtassers, die we voor het Amerikaanse leger bouwen, stonden die 300 uur in de ruwbouw, maar nu zitten we op zo’n 120 uur, met handlassers. In principe kunnen we hem met de robot in 24 uur aflassen’, illustreert Van Beek de tijdswinst die hiermee is te behalen. ‘Dan moet je nog wel wat nalassen en nabewerken. Maar dit is toevallig een oplegger waar heel veel lasmeters in zitten en waar je grote stukken kunt lassen. Dan biedt de robot heel veel voordelen.’ De aanschaf van de grote lasrobotinstallatie is onder andere met de grote defensieorders in het achterhoofd gedaan. Het voordeel van die orders is namelijk dat er grote aantallen per type order worden afgenomen, waardoor de robot niet telkens opnieuw geprogrammeerd hoeft te worden.
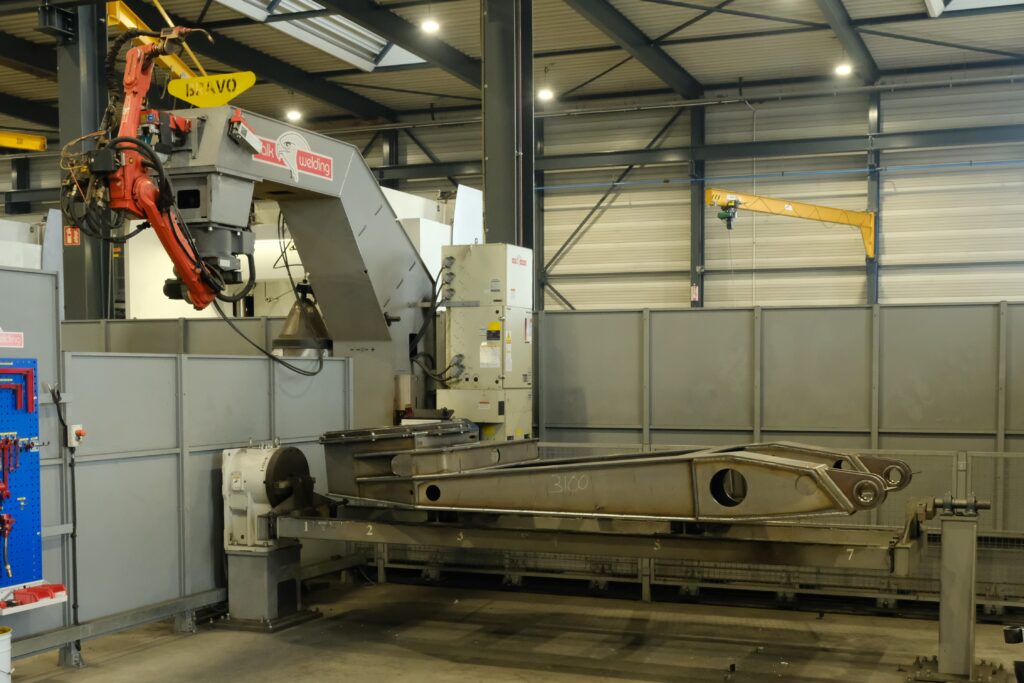
Er zijn overigens wel allerlei maatregelen genomen om ook in het geval van veel verschillende type opleggers, toch snel automatisch te kunnen lassen. Er is al geëxperimenteerd met automatische lasprogrammering. Maar er wordt ook gekeken naar de engineering van de modellen. ‘We zijn inmiddels zes jaar geleden begonnen met het formuleren van configurabele opleggers. Op dit moment is 80% van onze klantvraag al te beantwoorden met een standaard configurabele oplegger’, vertelt Van Beek. Maar hoewel opleggers voor klanten op elkaar lijken, lijken ze voor de productie en engineering juist helemaal niet op elkaar. ‘Dat is 140 jaar legacy’, legt ze uit. ‘Vroeger had een engineer heel veel ruimte om zijn eigen interpretatie van een oplegger te ontwerpen. Een vierasser werd heel anders opgebouwd dan een drieasser. Nu maken we juist alles modulair. We stoppen veel in een moedermodel en trekken zaken parametrisch op.’ De nieuwe drie- en vierassers worden zo op dezelfde manier opgebouwd. De basis is hetzelfde. Broshuis wil de inzet van de lasrobot verhogen en die robot is erbij gebaat dat bijvoorbeeld een nek van een oplegger altijd op dezelfde manier, van voor naar achter, wordt opgebouwd. De ene keer wordt hij wat langer dan de andere keer, maar dat maakt niet uit. Dan komt er gewoon één standaard sectie bij. ‘Op dit moment is dat nog niet het geval. Maar aangezien we de robotisering door willen zetten, zullen we heel kritisch naar het model moeten kijken.’
Kampen
Alle opleggers van Broshuis worden in Kampen geproduceerd en worden dan door de klant opgehaald. Als familiebedrijf wil de trailerbouwer ook een bepaald gevoel meegeven aan de klanten. ‘Het Broshuisgevoel’, zegt Van Beek. ‘In januari hebben we een open dag. Dan is er een route door te fabriek te volgen die het product ook aflegt. Dat begint bij het tekening maken. Dan wordt er snij- en zetwerk verricht. De buislaser staat aan. Daarna wordt er gelast. De lasrobots worden gedemonstreerd. En daarna is er de conserveringsstraat, die hebben we ook hier. Om uiteindelijk bij de afmontage een complete oplegger te kunnen laten zien’, besluit ze.
U moet inloggen om dit artikel te lezen
Onze unieke artikelen, analyses en expertise zijn speciaal voor u beschikbaar. Log in en lees verder!
Nog geen account? Meld u nu aan en krijg direct toegang tot exclusieve content.