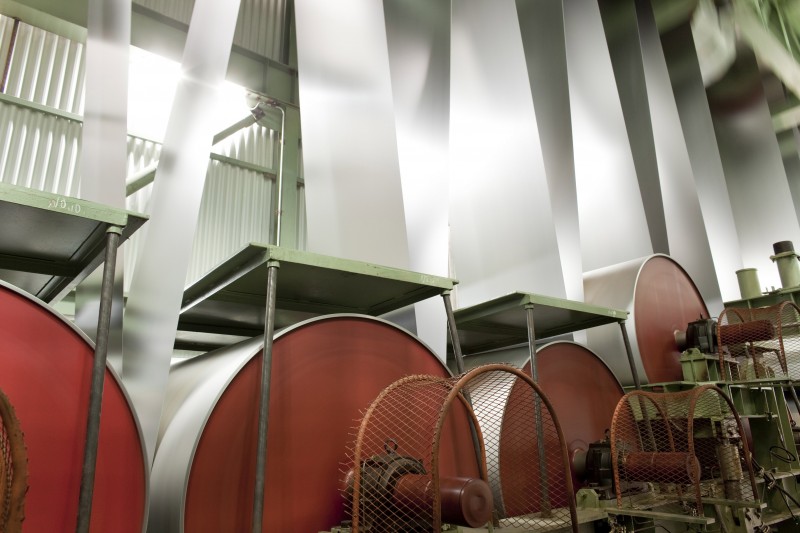
De noodzaak om gewicht te besparen stuurt de auto-industrie steeds meer in de richting van hoge sterktestalen. Dat stelt de staalproducenten én -verwerkers voor behoorlijke uitdagingen, onder andere op het gebied van laserlassen. Op het AKL 16 lieten zowel Outokumpu als machinebouwer SMS Group zien wat zij bereiken met laserlassen van deze staalsoorten.
Outokumpu Nirosta heeft twee varianten (ultra) hoge sterktestalen in het productportfolio, waar de autofabrikanten veel belangstelling voor tonen. Forta H800 is een koud gewalst product, een austenitische mangaan-chroomlegering. Forta H1200HP is een warm gewalste legering, een martensitisch chroomstaal met een hoog koolstofgehalte, een combinatie die het moeilijk lasbaar maakt. In het Forta H800 zit een percentage mangaan dat de fabrikant qua lassen voor de nodige uitdagingen stelt. De bijzonderheid is dat dit materiaal in de uiteindelijke toepassing sterker is dan de specificaties op het eerste gezicht doen vermoeden. ‘We verhogen de treksterkte door het laserlassen tot 1400 MPa en tijdens een crash verhoogt dit, door de energie die het materiaal inkomt, zelfs tot 2000MPa’, verduidelijkt Stefan Lindner van Outokumpu in Krefeld.
Sterker door opwarming
Dit laatste effect is wat hij noemt een zogenaamd ‘tweelingeffect’, officieel Twinning Induced Plasticity. Normaal gesproken is de lasnaad de zwakke plek in een lassamenstelling, maar in dit geval wordt de lasnaad bij een crash, waardoor er energie in het materiaal komt, juist nog harder. Volkswagen, de Outokumpu-klant die dit materiaal in de productie inzet, laserlast de crashzones met een 4kW fiberlaser met een snelheid van 6,4 m / minuut (plaatdikte 1,5 mm.
Laserlassen voor vijf minuten
Niet alleen de metaalverwerkende industrie past laserlassen toe, de staalbedrijven zetten deze verbindingstechniek ook in bij de productie van hun materialen. Christian Dornscheidt van de Duitse machinebouwer SMS Group schetste op het AKL 16 hoeveel moeite het soms vergt om een las te maken die slechts vijf minuten hoeft te houden. Het bedrijf ontwikkelt en bouwt complete staalfabrieken.
Omdat het beitsen en verzinken een continu proces is, moeten de coils die deze lijnen verwerken aan elkaar worden gelast. Daarvoor heeft SMS Group een laserlasunit ontwikkeld die op meerdere plekken in de wereld wordt gebruikt. Ook hier is de keuze voor de laser als verbindingstechnologie met name ingegeven door de opmars van hogesterktestalen. De lasverbinding zelf blijft slechts vijf minuten in stand: na het beitsen en verzinken wordt de lasnaad uit het materiaal gesneden. De belasting van de lasnaad gedurende deze vijf minuten is echter extreem hoog, schetste Dornscheidt. Zo’n lijn in Korea verwerkt per uur tien tot zestien coils die gelast moeten worden. De lijn, de snelste ter wereld, haalt een snelheid van 1200 meter per minuut en er komt een kracht op de lasnaad te staan van 1800 ton. ‘Productiestilstand betekent alleen op deze lijn een verlies van tienduizend euro per uur, zonder het verlies op de lijnen die hierna in het proces stilvallen’, aldus Dornscheidt over het belang van een robuust en betrouwbaar systeem.