Is het mogelijk om de grotendeels naar het verre buitenland verhuisde rubberproductie, deels, weer terug naar Nederland te halen, vroeg Richard Groot zich af. Met de nodige automatisering, waarom niet? Zes jaar geleden nam hij Artech Rubber uit Zutphen over om zijn plan mee te verwezenlijken.
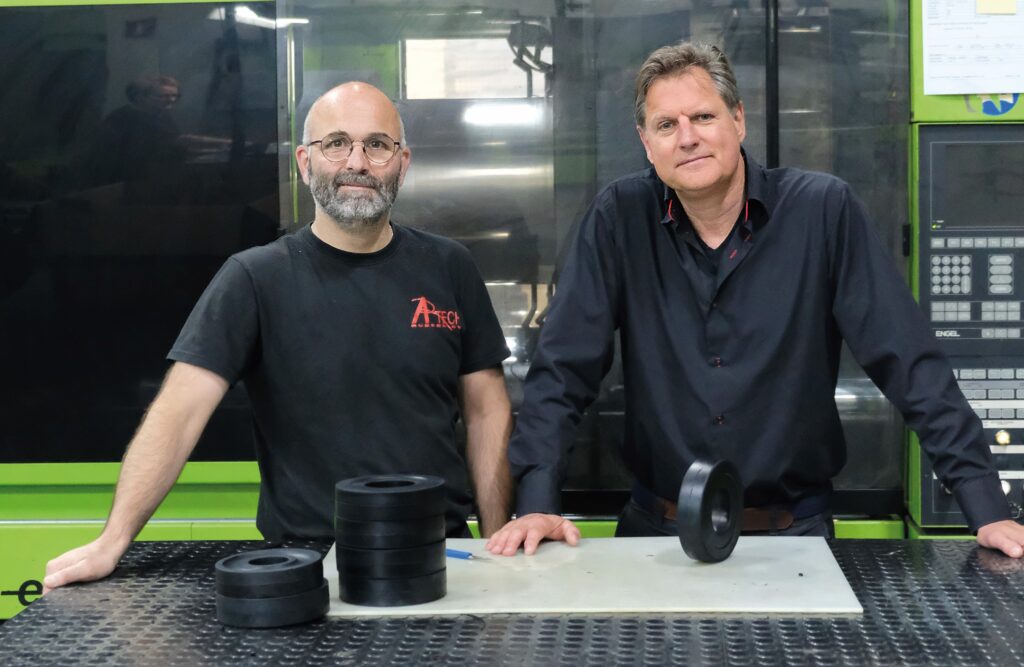
Richard Groot zag in de 27 jaar die hij werkte bij een grote handelaar in rubberproducten de rubberproductie verdwijnen van Noordwest-Europa, naar Zuid-Europa, en toen naar Oost-Europa en Azië. De behoefte naar rubber is alleen maar vergroot, maar de productie ervan verdween naar verre landen. Toen Artech Rubber, een bedrijf ingericht op kleinere series met korte levertijden, op zijn pad kwam, zag Groot mogelijkheden. ‘Ik dacht, als we hier met grotere machines en meer kunnen automatiseren, dan moet het mogelijk zijn om de productie van bepaalde rubberproducten terug te halen naar Nederland. Efficiënt en marge-technisch op een goede manier’, vertelt hij.
Overname
Kort na de overname, stopte een grote Duitse concullega met zijn rubberproductie. ‘Die hebben we toen ook overgenomen, waardoor we de beschikking kregen over een aantal verder geautomatiseerde en volautomatische rubber injectiemachines. Dat maakte dat we onze propositie naar de markt verder konden uitbreiden.’ Artech Rubber maakte altijd al relatief kleine series en klantspecifieke producten of specials, maar was nu ook in staat competitief grote series aan te bieden. Inmiddels is het zes jaar later, is Artech Rubber vier keer zo groot en groeide het personeelsbestand van acht naar ruim twintig medewerkers.
Verschil
Het verschil tussen de productie van rubber en dat van kunststof is aanzienlijk. Kunststof verwarm je tot het thermoplast zacht is, vervolgens wordt het gegoten in de juiste vorm en daarna afgekoeld. ‘Rubber werkt precies andersom. We moeten het rubber bakken om een vulkanisatieproces op gang te brengen waardoor je een veel langere cyclustijd hebt. Dat kan variëren van twee tot drie minuten tot wel een uur voor onze dikste producten. Al die tijd moet het product op constante temperatuur en druk worden gehouden en bezet het ook de pers natuurlijk’, omschrijft Groot.
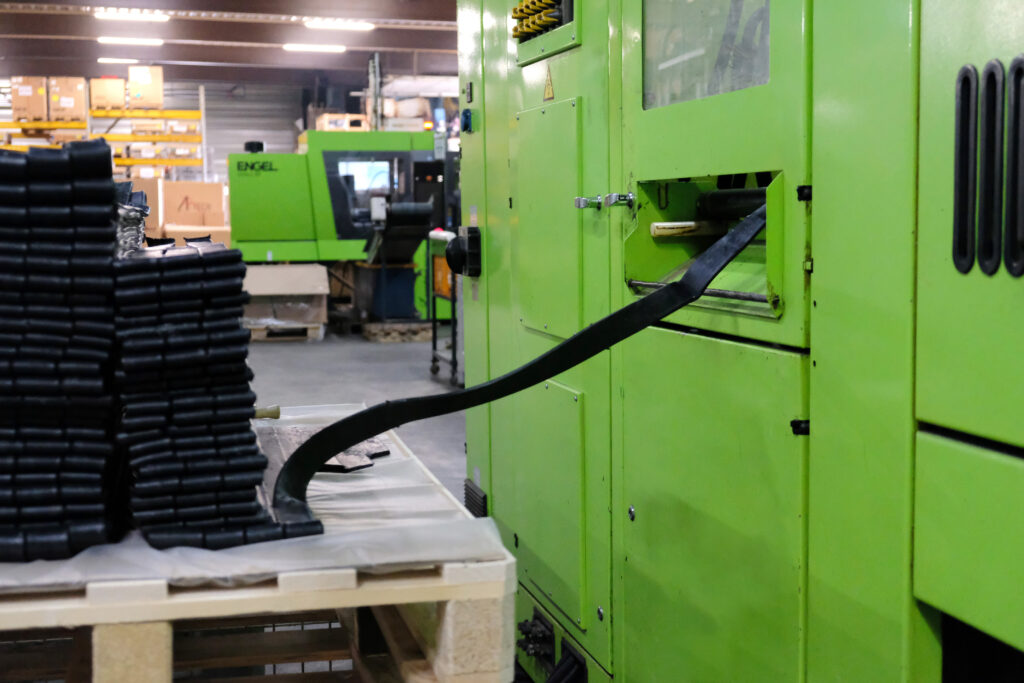
Matrijs
De matrijstechniek voor kunststof spuitgieten is lastiger. Wanddiktes moeten gelijk zijn en er zitten overal koelkanalen. Dat is voor rubbermatrijzen niet nodig. Omdat de cyclustijden zoveel hoger ligger, ga je voor rubber wel sneller kijken naar een matrijs waarmee je meerdere delen per cyclus produceert, dus met meerdere caviteiten. ‘We maken veel nieuwe producten en voor elk nieuw product heb je een matrijs nodig. We hadden al een matrijzenmakerij, maar maakten ook gebruik van uitbesteding. Inmiddels hebben we flink geïnvesteerd in twee nieuwe machines en maken we nagenoeg alle matrijzen zelf’, vertelt Groot. Artech heeft met de aanschaf van twee Style CNC-bewerkingscentra de capaciteit van de matrijzenmakerij verdubbeld. Ook het tekenen van de matrijzen in CAD-software gebeurt tegenwoordig intern. ‘Dan heb je het proces meer in eigen hand.’
Aantallen
Voor een proefserie maakt Artech een kleine proefmatrijs. ‘Blijven de aantallen klein, dan werken we met een enkelvoudige matrijs. Gaan die aantallen omhoog, dan gaan we naar een matrijs met meerdere caviteiten. Worden de aantallen nog hoger? Dan kijken we misschien naar injectie in plaats van het veel arbeidsintensievere conventioneel persen. Worden de aantallen nog hoger? Dan kunnen we kijken of we hem volautomatisch kunnen maken. Dan wordt het rubber geïnjecteerd en wordt de matrijs ook automatisch geleegd.’
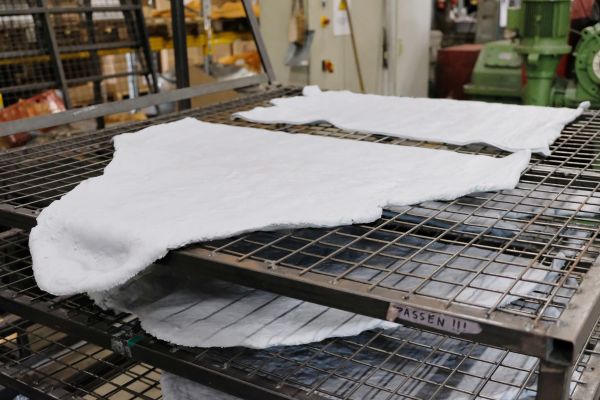
Breed
Artech wil breed operationeel zijn en richt zich daarom op zowel enkelstuks als kleine en grotere series. En kleine, maar ook grote producten. ‘Dat is juist onze markt’, zegt Groot. ‘Grote producten haal je niet gemakkelijk met de boot uit Azië. Daarnaast doen we veel rubber-metaal verbindingen. Bedrijven sturen dan hun metalen delen, die wij vervolgens berubberen. Ook iets wat je niet zomaar in Azië laat doen. Verder produceert Artech ook meer en meer producten voor een hoogwaardigere toepassing, waar meer en specifiekere eisen aan zitten. Te denken valt dan aan specifieke keuren, maar ook specialistische materialen zoals Aflas, siliconen en FFKM. Deze compounds worden deels in huis ontwikkeld door onze rubbertechnoloog en technisch directeur Dr. Ir. Kuno Dijkhuis.’
Soorten
Er is namelijk nogal wat variëteit in rubber en Artech ziet nagenoeg alle soorten langskomen, van natuurrubber (NR) tot EPDM en van NBR tot FFKM. Van natuurrubber, wat van rubberplantages komt, worden hoofdzakelijk banden gemaakt, een van de weinige producten die Artech niet produceert. ‘Natuurrubber is heel slijtvast, maar niet zo verouderingsbestendig’, weet Groot. ‘Dat moet je niet gebruiken voor raamrubbers, dan zijn ze zo weg. Daar kies je voor een synthetische rubber als EPDM. Ben je op zoek naar een voedingsmiddellenkwaliteit of werk je met stoom, dan kijk je vaak naar siliconen of Aflas. Je hebt ook kwaliteiten die uitermate geschikt zijn voor hydrauliek en pneumatiek, bijv. NBR of FKM. Daar werken we allemaal mee’, vertelt hij. Sommige rubbers waar Artech mee produceert, kosten drie euro per kilo en andere kosten vijfduizend euro per kilo.
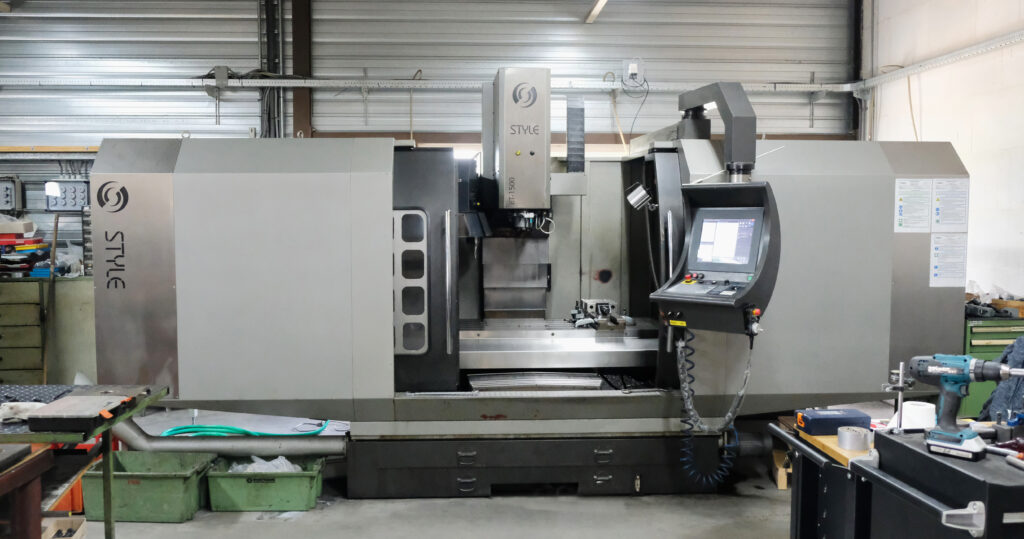
Zichtbaar
Rubberproducten in het algemeen, komen in tal van markten terecht, maar zijn in hun uiteindelijke functie overigens nauwelijks zichtbaar. Afdichtingen, die een groot gedeelte van de toepassingen van rubber vormen, zitten altijd ergens in en zie je dus niet. ‘In een verwarmingsketel, koffiezetapparaat of kraan zitten veel rubbertjes, maar die zie je niet.’ Artech maakt producten voor bijvoorbeeld pompen in de agrarische sector, maar ook voor de algemene maak- en voedingsmiddelenindustrie. In Nederland en soms daarbuiten.
Industrie
Technische directeur Kuno Dijkhuis signaleert dat de industrie het nog steeds lastig heeft. ‘We zien dat onze bestaande klanten iets minder doen. Maar we hebben veel aanvragen van nieuwe potentiële klanten en voor nieuwe projecten, dat zijn wel kansen.’
‘Vroeger was alles wat van ver kwam, lekker’, zegt Richard Groot weer. Maar dat is niet meer zo. ‘Vanwege duurzaamheid, corona, de blokkade van het Suezkanaal. Omdat een rubbermatrijs niet zo heel erg duur is, zeggen sommige bedrijven: ik wil voor vijftig procent van mijn behoefte een matrijs in Nederland hebben liggen. En die maken wij graag.’ Dijkhuis: ‘Dan hebben ze een tweede leverancier dicht bij huis, die ook in nood kan inspringen en opschalen. We hebben dan niet alleen de matrijs hier liggen, maar maken ook een bepaald percentage van de producten standaard. Dat is wel iets wat wij voor ogen hebben en wat we ook voor een groot aantal klanten al doen.’
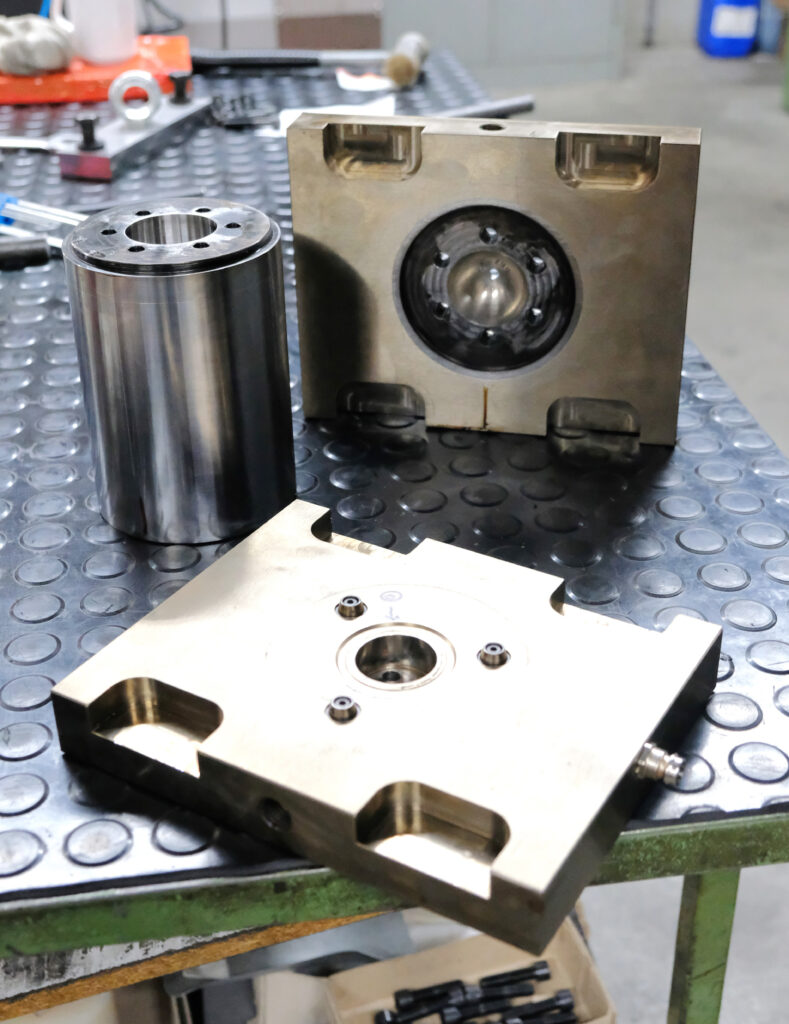
Recycling
Op het gebied van recycling is er ook met rubber van alles mogelijk en Artech is er volop mee bezig. Groot legt het proces uit: ‘Neem een autoband. De banden worden ingezameld en er zijn bedrijven die de producten goed kunnen sorteren en uit elkaar kunnen houden. De loopvlakken van die band worden eraf gehaald, gegranuleerd en gedevulkaniseerd. Dat devulkanisaat krijgen wij vervolgens binnen en daar kunnen wij nieuwe rubberen producten van maken, mits we daar de juiste ingrediënten aan toevoegen om het vulkanisatieproces weer op gang te krijgen.’ Omdat het rubber tijdens dit proces toch wat inboet aan kwaliteit en voor banden juist een hele hoge kwaliteit rubber is vereist, kan het vaak niet meer terug in zijn originele functie. ‘Rubber dat niet meer geschikt is om opnieuw als bandenrubber te gebruiken, kan nog wel gebruikt worden in andere producten, waarvoor de veiligheidseisen iets lager liggen.’
Probleem
De infrastructuur voor het recyclen van natuurrubber is redelijk goed op orde. Maar voor synthetische rubbers niet. ‘En bandengranulaat of devulkanisaat, wat 80 procent van de rubberconsumptie wereldwijd vormt, kan niet in een EPDM of NBR, dat moet terug in de band of in producten waarin gelijkwaardige rubbersoorten worden gebruikt’, weet Dijkhuis, die gepromoveerd is op het devulkaniseren van rubber. Er zijn nog geen partijen in de markt die synthetische rubbers verzamelen, sorteren, vermalen, granuleren en devulkaniseren. Dat is een probleem. ‘De bedrijven die dit voor de bandenwereld doen, vragen hoeveelheden van minimaal tien ton materiaal. Maar ik heb niet zomaar even tien ton productieafval liggen, want we doen er juist alles aan om het percentage afval zo laag mogelijk te houden’, legt Groot uit. Groot en Dijkhuis zijn dan ook blij dat de bijmengverplichting voor kunststoffen vanaf 2027, vooralsnog niet gaat gelden voor elastomeren. ‘We kunnen al heel veel. Maar we zijn ook beperkt, omdat we afhankelijk zijn van wat er vóór ons in de supply-chain gebeurt. Dat komt wel, maar dat kost tijd’, verwacht Groot. Inmiddels verwerkt Artech al zo’n 100 tot 150 ton gerecycled rubber per jaar. En daar gaat het gewoon mee door. ‘We blijven verbeteren en optimaliseren’, besluit Dijkhuis.