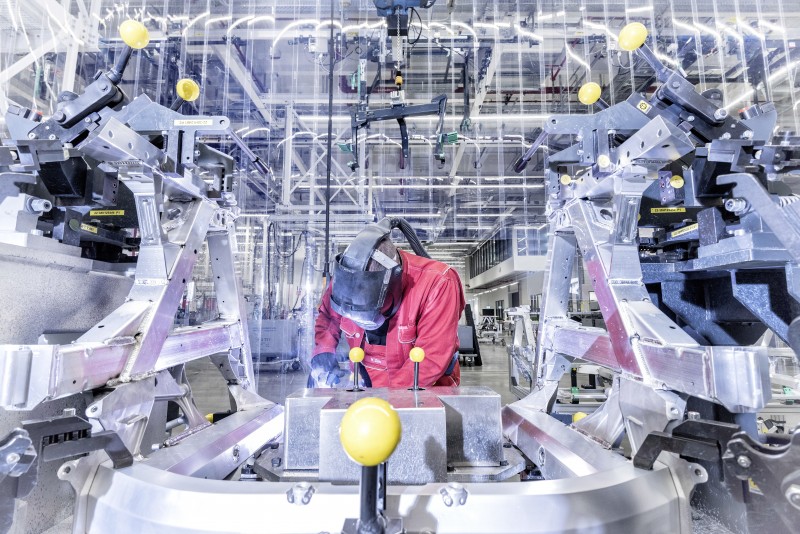
Verbindingstechniek is aan een omwenteling onderhevig: de toenemende mix van materialen in de carrosseriebouw en de groeiende toepassing van aluminium maken een andere manier van denken en doen noodzakelijk. Drijvende kracht hierachter is met name de automobielindustrie. Zij bepleit een verdere ontwikkeling van verbindingstechnologie en wil hierin snel resultaten zien. Dit betreft niet alleen zuivere aluminiumconstructies, maar ook de zogenoemde gemengde fabricage, bijvoorbeeld aluminium met staal of CFK, zo schrijven Nikolaus Fecht en Andreas Thoss in hun white paper voorafgaand aan Euroblech.
Niets gaat meer zonder lichte constructies. Dit wordt bevestigd door een actuele studie van de Duitse Landesagentur für Leichtbau Baden-Württemberg (Leichtbau BW). Volgens dit onderzoek zal de markt voor lichte constructies in de transportbranche tot 2020 op basis van recente prognoses tot 140 miljard euro stijgen. Dit betekent ongeveer een verdubbeling ten opzichte van 2010. Uit de studie komt naar voren dat de voertuigindustrie hierin een leidende rol vervult. Daarom werpen we een blik op het ‘automobielland’ Baden-Württemberg: daar vertrouwt inmiddels al 70 procent van alle automotive-ondernemingen op technologieën voor lichte constructies. Een voorbeeld hiervan is de Mercedes-AMG GT; zijn geoptimaliseerde spaceframe bestaat voor meer dan 90 procent uit aluminium componenten.
Spaceframe Audi met ponsklinknagels
Dit voorbeeld geeft de belangrijke rol van aluminium aan. De aanzet tot deze ontwikkeling gaf Audi al meer dan 20 jaar geleden met zijn ‘Audi Space Frame (ASF) – Concept Car,’ een Audi A8 met een carrosserie van aluminium. De Duitse autofabrikant sloeg destijds niet alleen met de ‘Body-in-White’ nieuwe wegen in, maar ook op het gebied van verbindingstechniek. Toen werd voor het eerst de werkwijze met het ponsklinken RIVSET van Böllhoff toegepast, waarmee via speciale klinkelementen in één keer twee of meer delen met elkaar verbonden kunnen worden, zonder eerst gaten te moeten boren. Volgens Böllhoff zelf werd in die tijd zo’n 70 procent van alle verbindingselementen volgens hun werkwijze geklonken. Met veel genoegen zagen de verbindingspecialisten in Bielefeld dat veel autofabrikanten voor hun aluminium en composieten met dunne wanden van lassen overstapten op ponsklinken en clinchen.
Toch is er ook sprake van een opleving van thermische verbindingsmethodieken. Dit geldt een brede range aan mogelijkheden. Zo ging het Institut für Schweißtechnik und Fügetechnik van de RWTH in Aken bijvoorbeeld het lassen met metaal- en wolfraam-inertgas (MIG/WIG) bestuderen, evenals met plasma, elektronen en laser (atmosferisch en onder vacuüm), RP-lassen en FSW-lassen. Naar gelang de toepassing, zijn voor het verbinden van aluminium delen in grote series volgens oberingenieur Dr.-Ing. Simon Olschok atmosferisch elektronenstraal- en laserlassen, MIG en FSW bijzonder goed geschikt.
Remote laserlassen
In de automobielindustrie zijn daarbij, afhankelijk van de taakstelling en de beoogde seriegrootte, met name twee methodieken in opkomst: remote laserlassen en weerstandlassen met een complexe procesvoering. Met betrekking tot de eerste sleepte de Audi-fabriek in Neckarsulm bij de Innovation Award Laser Technology 2016 de tweede prijs in de wacht voor het verder ontwikkelen van het remote laserlassen. De autobouwer gebruikte dit als eerste in de branche bij het verbinden van conventionele aluminium legeringen. In de praktijk heeft deze aanpak zijn nut al bewezen in de lichte carrosseriebouw (bijvoorbeeld bij de productie van deuren voor de Audi A8).
Tot nu toe gebeurde het laserlassen van monolithische aluminium verbindingen volgens teamcoördinator ‘Laserstrahltechnologie/Sensorik’, Jan-Philipp Weberpals, slechts ‘met tactiel geleide bewerkingsoptieken’. Het remote laserlassen levert ten opzichte van het tactiele laserlassen tijdsbesparingen van liefst 53 procent op, aldus Weberpals. Bovendien heeft deze methodiek als voordeel dat een gecontroleerde sturing van de temperatuur in het productiedeel mogelijk is. De precieze positionering van de laserstraal, in verhouding tot de laskant, verlaagt daarnaast het risico van vervorming en hittescheuren.
Weerstandslassen met complexe procesvoering
Thermische methodieken worden ook gebruikt door autofabrikant Ford in haar voortrekkersrol als het gaat om de eerste carrosserieën van 100 procent aluminium in grote series. Hier gaat het om de Pick-Up Truck F150, het meest verkochte voertuig in de VS. Bij de keuze voor een verbindingsmethodiek bij grote series, is de robuustheid van het fabricageproces van groot belang. ‘Omdat hier normaal gesproken geen of slechts zeer beperkt tijd beschikbaar is voor nabewerkingen’, aldus Michael Ölscher, research engineer Advanced Materials & Processes bij Ford Research and Advanced Engineering in Aken. Daarom vertrouwt Ford op het slimme samenspel van weerstandslassen met een complexe procesvoering, geïntegreerd onderhoud van de elektroden en geavanceerde lasapparatuur.
Onder de noemer ‘gemengde fabricage’ (multimateriaalmix), is de combinatie van staal met aluminium in de carrosseriebouw van voertuigen in opkomst. Tot de gangbare verbindingen in de lichte bouw behoren mechanische verbindingstechnieken, plakken en diverse combinaties. Sinds enige tijd streeft men ernaar de populaire combinatie aluminium/staal thermisch te verbinden. Een belemmerende factor zijn daarbij echter intrinsieke fenomenen als een te groot verschil van smelttemperatuur, duidelijke verschillen bij de coëfficiënten van warmte-expansie en de vluchtige verandering van het elektrochemische potentieel.
Deze problemen waren tot nu toe met behulp van hybride technieken vrij elegant op te lossen. Zo bleken bij de carrosserie van de Audi TT zogeheten ‘koude’ vormvaste en tegelijkertijd ook stofvaste verbindingen zeer functioneel. Daarbij gaat het om ponsklink- en schroefverbindingen, waarbij plaksel tussen aluminium en staal voor corrosiebescherming zorgt en tevens de stabiliteit van de verbinding versterkt. Tot de grootste uitdagingen bij het lassen van staal op aluminium behoren de harde en stroeve fasen die dan ontstaan. Om dit tegen te gaan werkt men in een door het Duitse Bundesministerium für Bildung und Forschung (BMBF) gedragen onderzoeksproject samen aan oplossingen. In dit zogeheten ‘LaserLeichter’ (ontwikkeling van op laser gebaseerde verbindingstechnologieën voor constructies van lichte bouw met verschillende materialen) onderzoekt men in het Laser Zentrum Hannover (LZH) een specifiek voor de verbinding aluminium/staal geschikt laserlasproces op maat.
De belangrijkste rol hierbij is weggelegd voor de spectroscopische controle van de inlasdiepte, zegt Stefan Kaierle, Head of Materials & Processes Department. ‘Want dit beperkt de vermenging van de elementen en zorgt daarmee voor een aanzienlijke verbetering van de eigenschappen van de lasnaden die erbij ontstaan.’ Dankzij de meting van de emissies van het plasma dat ontstaat, kunnen de onderzoekers op elk moment de benodigde inlasdiepte tijdens het hele proces bepalen en kan het vermogen van de laserstraal worden aangepast. Het LZH onderzoekt niet alleen verbindingen tussen aluminium en staal, maar ook tussen metaal en kunststof. Tot de methodieken daadwerkelijk in een productie-omgeving kunnen worden toegepast (het project loopt tot februari 2018), moeten producenten genoegen nemen met de huidige industrieel beproefde verbindingstechnieken. De bekende Trumpf Laser- und Systemtechnik noemt het remote laserlassen een ideale methodiek voor het ‘heet’ verbinden van aluminium en staal.
Lichtbooglassen: alternatief voor laser?
Een interessant alternatief voor de laser is het door Fronius ontwikkelde lichtbooglasprocedé CMT (Cold Metal Transfer), een doorontwikkeling van het MIG/MAG-lassen. In 2004 werd samen met staalfabrikant Voestalpine een aangepaste versie gebruikt om een voor vervorming geschikt halffabricaat van staal en aluminium te vervaardigen. Fronius heeft het CMT-proces, de naadgeometrie, het toe te voegen materiaal en de vervormbaarheid geoptimaliseerd. Het toe te voegen materiaal speelt een belangrijke rol. Dit bleek bijzonder geschikt bij een aluminiumlegering met 3 procent silicium en 1 procent mangaan (AW 4020). Volgens Fronius zorgt deze toepassing voor een ‘adequate vervormbaarheid, lage corrosiegevoeligheid en een positieve beïnvloeding van de samenstelling van de intermetaalfase (IMP)’.
1.000 mm per minuut
Deze methodiek heeft zichzelf bewezen bij het hechten van lichte aluminium delen aan de staalstructuur, waarvoor het conventionele puntlassen niet geschikt is. Het gaat om een tweezijdige las met een lasverbinding aan de aluminiumkant en een soldeerverbinding aan de verzinkte staalkant. Na jaren van gezamenlijke inspanningen slaagden Voestalpine en Fronius erin het verbindingsprocesproces van zo’n 300 tot 1.000 mm per minuut op te voeren. Maar de methode is in feite nog steeds te langzaam, aldus Karl M. Radlmayr MBA, Vice President Technology bij Voestalpine Metal Forming. In zijn optiek zou de verbindinsgsnelheid minimaal 3.000 mm per minuut moeten zijn. Daardoor pakt het ponsklinken met het oog op de totale kosten nog altijd voordeliger uit.
Conclusie
De ideale oplossing voor snel, proceszeker en kostentechnisch interessant verbinden is vooralsnog niet in zicht. Daarom moeten alle producenten die met aluminium en gemengde fabricage bezig zijn, van leverancier van grondstoffen en installatiebouwers tot de OEM’er, voor elke situatie de geschikte verbindingstechniek zien te vinden.
Deze white paper is geschreven door Dipl.-Ing. Nikolaus Fecht en Dr. Andreas Thoss als vooruitblik op Euroblech 2016. De publicatie is in het Engels en Duits te downloaden via:
• www.euroblech.com/english/white-paper
• ww.euroblech.com/deutsch/white-paper