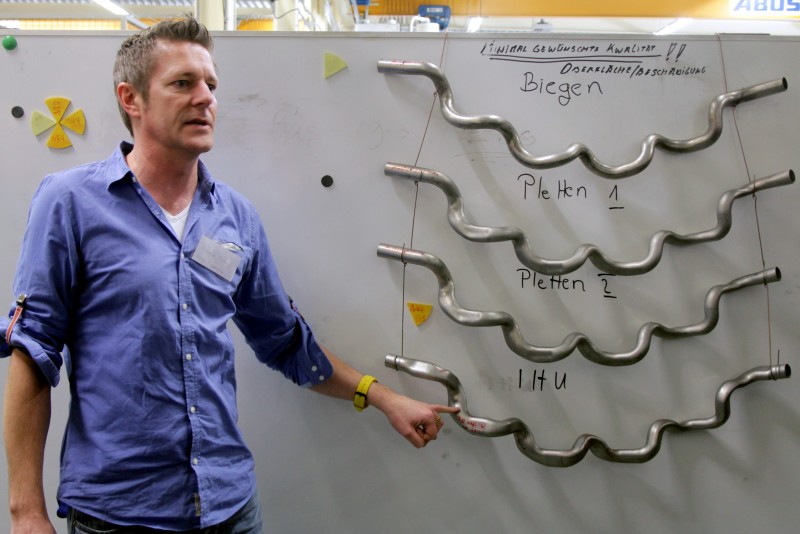
Hydrovormen is een vervormingstechniek om met vloeistof extreme geometrieën te vormen in buis en plaat. Hydrovormen is vooral bekend geworden bij het lichter construeren van buisvormige chassisdelen voor auto’s. In een pilot toont Hydroform Beheer aan dat het hydrovormen van een roestvaststalen draagarm tientallen procenten lichter uitvalt dan de conventionele draagarm van staal zoals VW die nu in zijn auto’s toepast.
Maurice Derhaag, technisch directeur Hydroforming vertelde over deze pilot tijdens de themabijeenkomst Hydroforming die Federatie Metaalplaat FDP medio maart organiseerde bij KISS Engineering, de holdingmaatschappij van Hydroform Beheer. Het bedrijf maakt in opdracht hydrovormproducten en hydrovormmachines.
Machines voor Rusland
Tijdens de themabijeenkomst stonden er twee Kiss hydroformmachines klaar voor transport naar Rusland, waar ze worden ingezet voor de productie van convectoren (zie onderstaande afbeelding).
Het hydrovormen wordt in Rusland ingezet om de lamellen die over een buis worden aangebracht te fixeren door de buis te hydrovormen. ‘Doordat wij zelf hydrovormen, nemen we die kennis mee in ontwerp en productie van de hydrovormmachines. Eventuele kinderziektes halen we er zodoende zelf al uit. Bedrijven kopen over het algemeen geen machine, maar een proces’, vertelt Math Slangen, algemeen directeur KISS Engineering en Hydroform Beheer.
Slangen is overtuigd van het belang van hydrovormen. Sinds 1988 houdt hij zich daar al mee bezig. Hydrovormen is dan ook vooral een kwestie van lange adem. Door vast te houden aan waarin je gelooft en door geduld kun je de industrie overtuigen van de betrouwbaarheid en reproduceerbaarheid van het hydrovormen. Hij noemt daarbij de drie-eenheid die bij het hydrovormen van groot belang zijn, te weten: de machine, de tooling en de kwaliteit van de buis. Als een van deze drie niet goed is, dan kun je het wel vergeten.’
Ervaring met hydrovormen
Na zijn korte inleiding gaf Slangen het woord aan zijn technisch directeur Maurice Derhaag, een techneut in hart en nieren. Tijdens de rondleiding, later die dag, vertelde Derhaag dat hij dat in 1994 aan de Universiteit Delft afstudeerde (bij professor Kals). De praktijk trok hem: ‘Ik wilde met mijn benen in de metaal staan, en dat doe ik nu bijna 21 jaar bij Hydroform Beheer.’ Kiss Engineering heeft veel ervaring met het hydrovormen van uitlaatsystemen. Ze maken onder andere uitlaten voor Bosal maar ze zijn ook second tier toeleverancier voor BMW, GM, Volvo Trucks, Mercedes en Ford. Steeds meer oriënteert Kiss Engineering zich op chassisbouw in de automobielsector. En daar is het credo voor de komende decennia: energiebesparing. Eén van de middelen daarvoor is door het gewicht van de auto omlaag te brengen.
Draagbalk
Tijdens de FDP themabijeenkomst legde Derhaag de nadruk op de pilot waarin het bedrijf een redesign in roestvaststaal heeft gemaakt van de stalen draagarm (wishbone), die Volkswagen nu toepast in de Polo (zie afbeelding onder).
Uitgangspunt was de bestaande draagarm van koolstofstaal. KISS Engineering koos voor een opzienbarende oplossing, namelijk roestvaststaal. Volgens Derhaag wordt het gebruik van rvs in deze constructies in de markt ‘absurd’ gevonden. Wij hebben met het hydrovormen veel ervaring met roestvaststaal. Zo produceren we voor GM de toevoerbuizen naar de katalysator voor alle 1,2 en 1,4 liter motoren (900.000 setjes voor 450.000 motoren) en voor de Volvo XC90 maken we de hitteschilden voor de uitlaatsystemen (350 per week). Voor de redesign draagarm koos Derhaag voor het austenitische rvs Wst 1.4301. De treksterkte van dit rvs is veel groter dan die van het conventionele koolstofstaal S420 MC_2. ‘Door te hydrovormen wordt dit voor rvs de treksterkte extra hoog als gevolg van koudversteviging. Een bijkomend voordeel is dat rvs een veel groter werkgebied heeft waarin je het probleemloos kunt vervormen’, vertelt de technisch directeur. Na trial en error kwam het bedrijf op het meest optimale eindproduct.
Daarbij zijn de volgende parameters van belang: startdiameter rvs 65 mm (staal 76 mm), eindwanddikte rvs 2,3 mm (staal 3 mm), vloeigrens verloopt na hydrovormen van 350 naar 832 N/mm2 (staal naar 603 N/mm2) dat is een 40 procent hogere vloeigrens dan die van staal. De wanddikte verloopt daarbij van 2,35 naar 2,08 mm (bij staal is dat van 3 mm naar 2,79 mm). Het rvs kan dus 27 procent dunner worden uitgevoerd dan het staal S420 MC_2. De totale gewichtsreductie is 34,4 procent. ‘Daar krijg je mensen wakker mee’, weet Derhaag. Hij merkt op dat ze de klant nog wel moeten overtuigen over het wijkgedrag en de crashbestendigheid van rvs. ‘En dat kunnen we: het wijkgedrag kunnen we tijdens het hydrovormen verbeteren door extra rillen in de draagarm te ‘blazen’. En voor wat betreft de crashbestandheid vertelt de technisch directeur dat rvs op voorhand elastischer is dan staal en zelfs binnen bepaalde grenzen beter bestand is tegen botsingen. ‘Het enige wat ons rest is om vertrouwen te kweken in het hydrovormen van roestvaststaal. Dat kunnen we bereiken door de markt te wijzen op de ontwikkeling in de uitlaten, die al jarenlang in rvs worden geproduceerd. Sterker, er worden geen stalen uitlaten meer gemaakt. Een uitdaging voor de toekomst is om de productontwikkelaars op de hoogte te brengen van de mogelijkheden van hydrovormen, want die ontbreekt nog bij de meeste engineers’, besluit Derhaag.