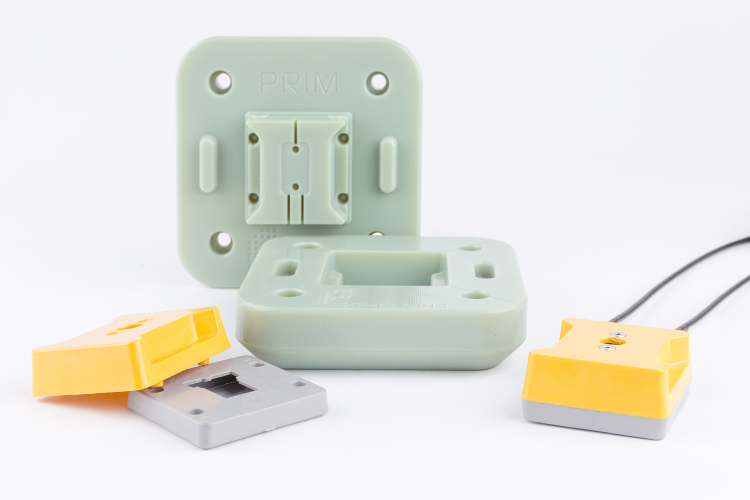
De verkopen van 3D-metaalprinters zaten vorig jaar behoorlijk in de lift. Wereldwijd althans, in Nederland blijft dit achter. De vraag is echter: moet het altijd metaal zijn? Of kan kunststof een betaalbaarder alternatief zijn, dat voor bepaalde toepassingen net zo goed is?
Onlangs hebben het Belgische Materialise en chemieconcern BASF een samenwerking aangekondigd. Het Duitse concern wil met de kennis en ondersteuning van Materialise nieuwe materialen gaan ontwikkelen, specifiek voor 3D-printen. Concreet gaat het op korte termijn al om een alternatief voor Ultem 985, een engineering plastic dat door Stratasys op de markt wordt gebracht. Ultem is op dit moment het enige materiaal dat gecertificeerd is voor toepassingen in de vliegtuigindustrie. Daar toont het zijn meerwaarde door het lage gewicht en het feit dat vliegtuigbouwers enkelstuks en kleine series kunnen printen, zonder investeringen in kostbare matrijzen. Airbus gebruikt dit materiaal onder andere voor de productie van kunststof cabinedelen voor de A350 XWB. Ultem is echter duur. Daarom wil BASF een goedkoper alternatief ontwikkelen. Men rekent erop dat 3D-printen met kunststoffen dan breder in de industrie ingezet gaat worden.
Nylon CF12 vervangt metaal
Want Ultem leent zich net als een ander Stratasys materiaal, Nylon 12CF, heel goed voor de productie van bijvoorbeeld machineonderdelen die nu nog vaak uit aluminium worden gefreesd. Het gaat hier om een filament dat met koolstofdeeltjes is gevuld (35% vulling) en hierdoor een hoge stijfheid heeft. Visual First, een Nederlands engineeringbureau, heeft een poos geleden besloten om een bepaald machineonderdeel uit een productielijn van The Chocolate Factory in Rotterdam met dit materiaal te printen. Tot nog toe werden de onderdelen handmatig gemaakt uit plaatdelen. Deze hebben een lange levertijd. Omdat ze regelmatig verbuigen, ligt de lijn dan stil. ‘Met de Stratasys 3D-printer kunnen we op maat gemaakte vervangingsonderdelen on demand produceren. En deze zijn net zo effectief als de metalen componenten’, legt Carl van der Rijzen van Visual First uit. ‘We printen en leveren de onderdelen binnen een week aan The Chocolate Factory, wat van vitaal belang is voor de continuïteit van hun productielijn.’ De geprinte onderdelen zijn bovendien aanzienlijk lichter dan het metalen onderdeel en kosten gemiddeld 60 procent minder.
Stratasys heeft dit jaar ook een nieuwe kunststof voor de FDM-printers gelanceerd, Antero 800NA. Dit zogenaamde PEKK-materiaal is, behalve dat het goede mechanische eigenschappen heeft, ook chemisch resistent. Hierdoor kan het bijvoorbeeld in de offshore industrie worden toegepast. Het nieuwe materiaal komt later dit jaar beschikbaar voor de twee duurste FDM-printers van Stratasys, de Fortus 450 en 900mc.
Opspanmiddelen
Maakbedrijven die de mogelijkheden van 3D-printen willen verkennen, kunnen ook beginnen met opspanhulpmiddelen te 3D-printen. Dit is een relatief eenvoudige stap, die weinig investeringen vergt en waarmee wel goede resultaten behaald kunnen worden. Mark Burghoorn, AM-consultant bij Cards 3D Printing Solutions in Best, heeft al enkele tientallen maakbedrijven op weg geholpen vanuit het Ultimaker 3D-Printing Experience Center.
Mark Burghoorn: ‘De investeringswaarde van deze 3D-printers is voor deze sector niet spannend. Waar het om gaat, is dat engineers snel enthousiast raken en leren hoe ze goede prints maken.’ Kortere doorlooptijden en lagere kosten zijn twee van de grootste voordelen die maakbedrijven hieruit halen. Met het juiste design en de goede printerinstellingen, kun je volgens hem opspanmiddelen printen die in de praktijk van alledag hun werk goed doen.
Een fabrikant die eveneens sterk inzet op het 3D-printen van opspanmiddelen is het Amerikaanse Rize. Sinds kort vertegenwoordigt Aga 3D-Color Solutions in de Benelux dit Amerikaanse merk, dat zich qua technologie onderscheidt van de rest. Rize heeft een eigen 3D-printtechnologie die ervoor zorgt dat de producten in alle richtingen nagenoeg dezelfde mechanische eigenschappen hebben. Met filament geprinte onderdelen zijn namelijk in de Z-richting zwakker. Dat moet je met het ontwerp opvangen. Rize heeft hier geen last van. Eerder dit jaar op RapidPro toonde het daarom lasmallen die deels 3D-geprint zijn. Een derde voorbeeld is te vinden bij Markforged, het Amerikaanse bedrijf dat enkele jaren geleden de technologie introduceerde om een koolstofvezeldraad mee te printen in een verder met filament geprint onderdeel. Het levert sterke onderdelen op, onder andere voor het gebruik van klemmen voor in de verspanende industrie.
Spuitgietmatrijzen printen
Een heel andere toepassingen van 3D-printen met kunststof is het maken van spuitgietmatrijzen. Matrijzenmakers moeten deze ontwikkeling in de gaten houden. Enerzijds omdat er een deel van hun markt kan verdwijnen, anderzijds omdat het een kans voor hen is. In Nederland is P3D een van de koplopers op dit vlak. Het nog jonge bedrijf is opgericht door Promolding om de Printed Injection Mold (PRIM) technologie verder uit te rollen. P3D print met een Objet machine van Stratasys spuitgietmallen, waarmee enkele tientallen producten gespuitgiet kunnen worden. Pascal Willems, design engineer bij P3D, zegt dat PRIM een gat vult tussen prototyping en productie.
‘Printerfabrikanten komen met hun materialen in de buurt van de echte kunststoffen, maar een ABS like is geen echt ABS. Het blijven altijd imitatiematerialen.’ Het kost ongeveer een week om vanaf een ontwerp de eerste serie van enkele tientallen spuitgietproducten (maximaal formaat 30 bij 30 cm) klaar te hebben, in de kunststof die de klant in het definitieve product wil toepassen. ‘Dit kan echt op geen andere manier.’ Deze technologie leent zich eveneens voor hele kleine series. En aan het einde van de levenscyclus van een product, als er alleen nog reserveonderdelen nodig zijn. In plaats van dure voorraden aan te houden, kan men dan de mal printen en de onderdelen spuitgieten.
Technisch kan er veel, maar bepaalde zaken moet je anders oplossen. Zo kun je bijvoorbeeld geen schuif printen voor het lossen van het product uit de mal. De oplossing van P3D is dat de mal uit meerdere delen wordt gemaakt. Pascal Willems houder over deze ervaringen op de Kunststoffenbeurs 2018 een presentatie. Internationaal doet onder andere Schneider Electric hetzelfde. De France producent van elektronicacomponenten gebruikt de lasersinter machines van Prodways voor het 3D-printen van spuitgietmatrijzen. Daarmee spuitgiet het vervolgens met glasgevuld polyamide. Doel hiervan is de doorlooptijd in de productontwikkeling terug te brengen, doordat men voor de certificeringen niet meer weken hoeft te wachten op aluminium matrijzen.
Verloren wasgieten
3D-metaalprinten is complex en vergt hoge investeringen. Dat weerhoudt tot nog toe veel maakbedrijven om in te stappen. Via een omweg is er echter ook veel mogelijk. Waarom geen gietvormen en kernen 3D-printen om via de verlorenwasmethode tot een fijngietstuk te komen? Een indirecte weg, maar het leidt wel tot goede producten, biedt designvrijheid en scheelt doorlooptijd vergeleken met de traditionele technieken voor het maken van gietkernen en -vormen.
Dit is een andere oplossing dan het zandprinten, zoals dat in Nederland onder andere door Sanders wordt gedaan. DSM Somos heeft hiervoor speciale materialen ontwikkeld, die na het wegbranden van de kern heel weinig residu achterlaten. Een van de sectoren waarin dit al vrij standaard begint te worden, is de sieradenindustrie. Het Franse Prodways heeft daarom onlangs nog Solidscape overgenomen dat met een eigen 3D-printtechnologie zich specifiek op de toepassingen van verloren wasgieten richt.
Solidscape werkt met zeer fijne druppels en een resolutie van 5.000 bij 5.000 dpi. Daarnaast wordt elke printlaag nabewerkt. Dat resulteert in een zeer gedetailleerd model dat vervolgens gebruikt wordt voor het verloren wasgieten van zowel sieraden als fijnmechanische componenten. En die kunnen dan heel complex zijn, complexer dan met mechanische bewerkingstechnieken maakbaar is.
3D-printen: de stand van zaken
Er wordt veel geroepen en geschreven over 3D-printen. De echte doorbraak laat echter nog op zich wachten, afgezien van sectoren zoals de luchtvaartindustrie en de medische sector waar de technologie wel zijn weg naar serieproductie begint te vinden. Deze zomer brengt Vraag & Aanbod een serie artikelen waarin zowel wordt ingegaan op de ontwikkelingen bij de verschillende technieken en materialen maar waarin ook de relatie wordt gelegd tussen smart industry en 3D-printen. Zorgt de digitalisering van de maakindustrie er uiteindelijk voor dat 3D-printen een standaard productietechnologie wordt?
Eerder (Vraag & Aanbod, week 28/29) verscheen al een artikel over Direct Energy Deposition, zoals de officiële term is voor 3D-lasercladden . In deel 2 (Vraag & Aanbod, week 30/31) werd ingegaan op goedkopere alternatieven voor het klassieke poederbed proces. Deel 3 (dit verhaal dus) gaat over het printen met kunststof, dat in een toenemend aantal toepassingen een volwaardig alternatief voor metalen onderdelen kan opleveren. Het slot – deel 4 – dus – geeft vier redenen om te gaan 3D printen.