Interregconsortium BeamPipes4ET ontwikkelt een techniek voor een onafgebroken productie van stalen buizen en de montage ervan onder de grond. De technologie speelt een rol voor de bouw van de Einsteintelescoop, waar 120 kilometer aan vacuümbuizen voor nodig zijn.
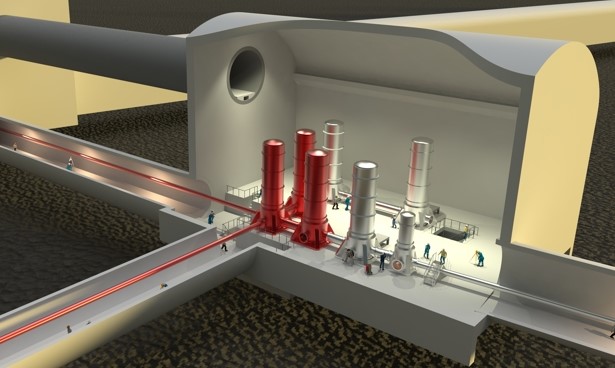
Traditioneel worden vacuümbuizen in fabrieken geproduceerd in secties van maximaal 18 meter lang. Vervolgens worden ze naar de plaats van gebruik getransporteerd en ter plaatse met flenzen of lasnaden aan elkaar verbonden.
BeamPipes4ET kiest ervoor aanpak om deze buizen op locatie te produceren. Door rollen plaatstaal te gebruiken kunnen buizen van honderden meters lang uit één stuk worden gemaakt. Het project ontwikkelt hiervoor een geautomatiseerde robot die zich door de buizen verplaatst.
Omdat de productie op locatie plaatsvindt is er veel minder transport nodig vergeleken met de traditionele manier van buizen transporteren. Rollen plaatstaal transporteren is namelijk efficiënter dan buizen transporteren die op locatie nog aan elkaar verbonden moeten worden.
Nieuwe lastechnologie
Het project ontwikkelt ook een nieuwe technologie voor het lassen van buizen. Bij het lassen hebben lasoppervlakken en hun omgeving een wisselwerking met elkaar. Door met de geautomatiseerde robot onder een mobiel vacuüm te laserstraallassen vermindert die wisselwerking sterk.
Uiteindelijk worden de uiteinden van de buizen voorzien van flenzen en aftakkingen voor pompen en andere verbindingen. Dit wordt mogelijk gemaakt door een technologie om deze onderdelen uit het ruwe metaal te trekken.
Van samenwerking naar concrete toepassingen
De basis voor deze samenwerking werd gelegd in het Interreg Maas-Rijn-project ET2SMEs, waar de Belgische Provinciale Ontwikkelingsmaatschappij Limburg bedrijven hielp om grensoverschrijdende partnerschappen aan te gaan. Dit leidde tot een samenwerking tussen het Belgische Aperam en Werkhuizen Hengelhoef, het Duitse FEF en RWTH Aachen University. Samen ontwikkelden ze het principe van ondergronds vacuümbuizen produceren, via laserlassen en met minimale milieubelasting.
Na een succesvolle onderzoeksfase wordt deze technologie nu opgeschaald binnen het BeamPipes4ET-project, dat een budget van 2,8 miljoen euro heeft, waarvan de helft afkomstig is van Europese subsidies. Door UHasselt, de Universiteit Antwerpen en het Nederlandse bedrijf SBE toe te voegen aan het consortium, wordt de technologie verder verfijnd en in de praktijk gebracht.
Limburgse staalindustrie maakt zich op voor toekomst
Een groot deel van de activiteiten vindt plaats in Belgisch Limburg. Werkhuizen Hengelhoef ontwerpt en bouwt de mobiele lasrobot, terwijl Aperam de grondstoffen voor de buizen levert. De lasapparatuur, ontwikkeld door FEF , wordt uitvoerig getest door UHasselt.
‘Aperam biedt technische ondersteuning aan dit project door advies te verlenen over de verschillende keuzemogelijkheden inzake staalsoorten. Onze doelstelling is dat één van onze eigen producten in het project een belangrijke rol zal spelen. Aperam roestvast staal is gemaakt uit gerecycleerd materiaal. Dit betekent dat elke Limburger, als de telescoop er komt, zal hebben bijgedragen met elke kilo inox die hij/zij via het containerpark in het recyclage circuit heeft gebracht. Zo wordt de Einsteintelescoop eigenlijk iets waar ieder van ons een stukje aan heeft bijgedragen’, aldus Jimmy De Wilde, plant general manager van Aperam Genk.
‘Bij UHasselt zetten drie onderzoeksgroepen hun schouders onder dit project. Aan de hand van hun complementaire onderzoeksexpertise zullen zij de lasnaden van het kilometerslange, ondergrondse vacuüm buizensysteem zowel fysisch, mechanisch als microscopisch controleren om zo de optimale kwaliteit van de naden te kunnen garanderen’, gaat professor Ronald Thoelen, decaan van de Faculteit Industriële Ingenieurswetenschappen UHasselt verder.
De buizen van BeamPipes4ET kunnen ook gebruikt worden voor grote vacuümsystemen, pijpleidingen of andere grote leidingsystemen.