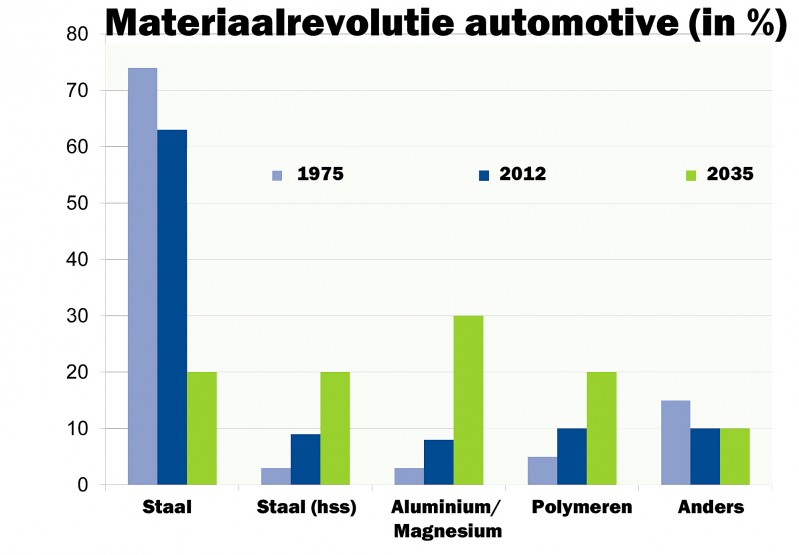
Staal is de grote verliezer in de automobielindustrie. Het aandeel hogesterktestaal groeit weliswaar sterk, maar dat maakt de teruggang van het aandeel staal in een auto niet goed. Aluminium en magnesium blijven daarentegen op groeipad, vooral in gietstukken.
Dat blijkt allemaal uit een studie van IKB Deutsche Industriebank, naar aanleiding van de gieterijbeurs GIFA. De traditionele gieterijen bijten echter van zich af.
Eén grafiek schetst eigenlijk de hele materiaalrevolutie die zich in enkele decennia tijd in de automobielindustrie voltrekt. In 1975 nam staal nog meer dan 70 procent van alle materialen in een auto voor zijn rekening. In 2035 zal dit nog slechts 20 procent zijn, denken de onderzoekers van IKB Industriebank, die de ontwikkelingen in de gietindustrie in kaart brachten. Hogesterktestaal zal tegen die tijd eveneens 20 procent voor zijn rekening nemen. Samen 40 procent dus, bijna een halvering. Liefst 30 procent van de materiaalmix in een personenauto komt tegen 2035 voor rekening van magnesium en aluminium. En 20 procent voor polymeren en composieten, net zoveel als conventioneel staal dus.
Deze ontwikkeling wordt ingegeven door de vraag naar reductie van energieverbruik en CO2-uitstoot. Lichtmetaal wint daarbij aan belang, net zoals carbon.
Gewicht nog verder omlaag
Deze trend weerspiegelt zich ook in de ontwikkeling die de onderzoekers schetsen voor de gieterij-industrie. Behalve dat de gieterijen zich er op moeten instellen dat de groeimarkten in het Oosten liggen, krijgen ze ook nog eens te maken met de materiaalverandering. De onderzoekers verwachten dat de Duitse aluminiumgieterijen al heel snel door de grens van 1 miljoen ton aluminium gietproducten heen gaan. Vooral in Oost-Europa groeit deze markt. Daarentegen blijft de Europese markt voor ijzer- en staalgieterijen zeker tot 2020 stabiel. China, India en de VS zijn hier de winnaars. China groeit overigens ook wat betreft de aluminiumgietindustrie. De IKB Deutsche Industriebank zegt in haar onderzoek verder dat het absoluut noodzakelijk is dat Europese gieterijen hun technologische koppositie vasthouden. De stuksgewichten van de gietdelen moet verder omlaag. Daarnaast zullen ze moeten investeren in compleet bewerken, want OEM’ers kiezen voor een one-stop-shoppingmodel.
Alternatief voor plaatwerk
Gietwerk snoept wel aandeel af van zowel smeeddelen als plaatwerkdelen. Vooral bij personenauto’s worden plaatdelen voor het chassis vervangen door complexe gietproducten. Een goed voorbeeld hiervan toonde de American Foundry Society op Newcast. Het gaat hier om een onderdeel voor de voortrein van een auto, gemaakt van aluminium Aural 5S-T5 met hogedruk vacuümgieten. Het project is samen met Magna International en Ford opgezet en heeft ertoe geleid dat vijf plaatpersdelen vervangen zijn door één gietstuk. Daarmee realiseert American Foundry Society 25 procent gewichtsbesparing. Het onderdeel wordt toegepast om het chassis te versterken en extra stijfheid toe te voegen.
Gietijzer zo licht als aluminium
De ijzergieterijen laten zich echter niet uit het veld slaan. IJzergieterij Fritz Winter uit Stadtallendorf toonde samen met het Oostenrijkse AVL op Newcast een studie naar hoe je met gietijzer lichter kunt gieten, mits je hiervoor ontwerpt en de nieuwe giettechnologie inzet. Ze hebben als uitgangspunt het cilinderblok van een verbrandingsmotor met een inhoud van 1.600 cc genomen. Door het ontwerp aan te passen aan de moderne giettechnologie, zoals 2,5 mm dunne wanden, en compacter te ontwerpen, slaagt men erin om het gietijzeren blok bijna net zo zwaar (of licht) te maken als een aluminium blok: 132 kilo voor het gietijzeren blok tegen 130 kilo voor het aluminium. Kijk je naar het hele productieproces, dan is de benodigde hoeveelheid energie voor het gietijzeren blok lager dan voor de lichtmetalen blokken, onder andere doordat geen warmtebehandeling nodig is. Men gebruikt voor het gieten 100 procent staalschroot, dat wereldwijd in ruime mate beschikbaar is. Met het nieuwe gietproces dat men heeft ontwikkeld, giet Fritz Winter met een tolerantie van 0,8 mm en een minimale wanddiktetolerantie van 0,5 mm.