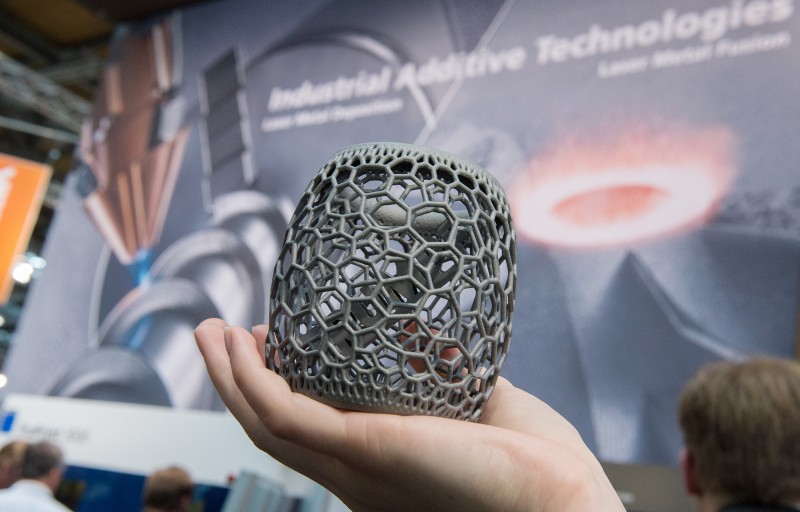
Afgelopen jaar zijn er wereldwijd miljoenen onderdelen 3D-geprint. Het grootste gedeelte is nog steeds een prototype. Maar een toenemend aantal vervangt een product dat tot nog toe is gefreesd, gedraaid of wellicht een samenstelling van metalen onderdelen is. Waarom vervangen machinebouwers samenstellingen door 3D-geprinte onderdelen? En kan kunststof als alternatief dienen voor metaal?
3D-printerfabrikant HP toonde op de Hannover Messe enkele voorbeelden van machinebouwers die hun klassieke productietechniek vervangen hebben door het 3D-printen met PA12, een industrieel veel gebruikt nylon. Een van deze voorbeelden is een onderdeel voor een industriële boor, tot voor kort samengesteld uit acht losse componenten. Hieronder enkele freesdelen, enkele met laser gesneden plaatdelen en twee licht gebogen en afgezaagde buizen. Deze acht onderdelen moeten geassembleerd worden, deels met schroefverbindingen. Totale kosten: 417 dollar.
Deze acht maakdelen werden vroeger samengesteld tot één machineonderdeel. (Foto: Franc Coenen)
HP heeft het oorspronkelijke ontwerp aangepast voor de multijet fusion printtechnologie. Dit onderstreept waarom 3D-printen pas zinvol is als het ontwerp hiervoor wordt aangepast. Het nieuwe onderdeel kan namelijk in één keer worden geprint. Assemblagekosten vallen dus helemaal weg. Er hoeft slechts een 3D-CAD file op voorraad te zijn: daarmee kan snel op de vraag worden ingespeeld. Voorraadkosten vallen dus eveneens weg. Het 3D-printen van het onderdeel kost volgens HP 20,29 dollar. Uiteraard rekent de fabrikant hierbij met een optimale vulling van de 3D-printer. Is dat niet mogelijk, dan vallen de kosten hoger uit. De eerlijkheid gebiedt te zeggen dat waarschijnlijk vaker met een niet optimale vulling wordt geprint dan wel. Maar zelfs als daarmee rekening wordt gehouden, zijn de productiekosten vele malen lager dan wanneer het onderdeel met de klassieke technieken wordt gemaakt. Het gewicht nam eveneens met 93 procent af, wat in de machinebouw een belangrijk voordeel kan zijn. Deze gewichtsreductie komt allereerst door het gebruik van kunststof en doordat 3D-printen zich als geen andere techniek leent voor topologie optimalisatie.
Instant tooling bij NTS
Een ander voorbeeld hoe je met relatief eenvoudige 3D-printtechnologie freesdelen kunt vervangen, is te vinden bij NTS in Eindhoven. Een jaar geleden is de high tech system supplier gestart met het 3D-printen van opspangereedschappen, onder andere voor de assemblage en de meetkamer. Een van de eerste voorbeelden is een persblok, dat gebruikt wordt om twee onderdelen in elkaar te persen.
Jarenlang heeft NTS dit gemaakt van een freesdeel met daarop een klem gemonteerd. De klem was een koopdeel, het aluminium blok werd intern gefreesd. Het ontwerp is aangepast aan de mogelijkheden en eisen van 3D-printen en tegenwoordig 3D-print NTS het gereedschap op een Ultimaker S5 met Ultimaker Tough PLA. Dit blijkt in de praktijk voldoende sterk te zijn. Kostprijs van het ge-3D-printe gereedschap: 30 euro; kostprijs van het oorspronkelijk gefreesde gereedschap: 200 euro. In beide berekeningen zitten ook de engineeringkosten. Bijkomend voordeel is dat men veel flexibeler is: het 3D-geprinte gereedschap is binnen een dag beschikbaar. En de freesmachines blijven beschikbaar voor opdrachten van klanten.
Groei van 3D-printen
De verwachtingen over de groei van 3D-printen lopen nogal uiteen. De voorspellingen voor de komende vijf jaar lopen uiteen van een groei tussen de 18 en 27 procent per jaar. Gemiddeld betekent dit dat tussen nu en 2024 de groei elke drie jaar qua omvang zal verdubbelen. Dat gaat elk jaar dus om miljarden euro’s. Maar afgezet tegen de totale omvang van de wereldwijde markt voor de maakindustrie, heeft 3D-printen nog steeds een aandeel van minder dan 0,1 procent. Dat zou echter wel eens kunnen veranderen, schrijft het management van het Amsterdamse platform voor maakproducten 3D-Hubs in de meest recente analyse. Tot nog toe hebben bedrijven 3D-printen vooral voor prototyping ingezet. Die markt is slechts enkele tientallen miljarden dollars groot. Uit interviews die 3D Hubs heeft gehad met grote ondernemingen leiden zij af dat de grote bedrijven de eerste stappen zetten richting kleinschalige productie met 3D-printen en sommige zelfs richting massaproductie. Deze markten zijn 10 tot 100 keer groter dan de prototyping markt en daar ontstaan dus nieuwe kansen voor de 3D-printindustrie. Een marktaandeel van 1 procent in de totale maakindustrie is dan ook niet onrealistisch, aldus 3D Hubs. Dat zou een 3D-printmarkt opleveren die vijf keer groter is dan de meest optimistische voorspelling.
Afgelopen jaar werden er in Europa meer dan 250.000 onderdelen ge-3D-print via het 3D Hubs platform. Het leeuwendeel hiervan werd besteld door bedrijven in het Verenigd Koninkrijk (42%), gevolgd door Duitsland, Nederland en Frankrijk. In de VS werden overigens via het platform meer dan 350.000 onderdelen besteld.
Mallen printen en niet frezen
Een andere toepassing waarbij 3D-printen het CNC-frezen zou kunnen gaan verdringen, is de productie van mallen voor composietdelen voor bijvoorbeeld de vliegtuigindustrie. Dit is een van de toepassingen waarop CEAD uit Delft zich richt. Het Nederlandse bedrijf heeft recent de eerste twee groot formaat 3D-printers voor het printen van kunststof versterkt met continue koolstofvezels aan klanten uitgeleverd.
Lucas Janssen, mede-oprichter, ziet toepassingen van deze technologie in bijvoorbeeld de productie van stempels en matrijzen. ‘Normaal worden deze gefreesd van speciaal gereedschapstaal omdat men een uitzettingscoëfficient wil die dichtbij die van het composietmateriaal ligt. Printen met fibers is dan de oplossing. Hiermee vervangen we metaal door kunststof bij de matrijzen.’ CEAD onderzoekt op dit moment samen met het Koninklijke NLR deze toepassing.
Deze acht maakdelen werden vroeger samengesteld tot één machineonderdeel. (Foto: Franc Coenen)
Metaal vervangen door kunststof
Kun je metalen componenten zonder meer vervangen door kunststof delen? Nee, niet altijd. Maar de kunststofproducenten ontwikkelen steeds betere materialen voor 3D-printen en door het ontwerp aan te passen, kan een ge-3D-print onderdeel op kritische punten versterkt worden. Daarnaast worden in de machinebouw veel aluminium frees- en plaatwerkdelen ingezet, die amper worden belast. In dat geval is het vervangen van het lichtmetaal door een kunststof vaak wel haalbaar.
Zehavit Reisin, bij Stratasys verantwoordelijk voor materiaalontwikkeling, ziet deze omslag op gang komen. ‘Dat is niet gemakkelijk, het vergt een andere mindset. Als bedrijven de technologie eenmaal ontdekt hebben, gaat het snel.’ Zij merkt dat momenteel vooral grote bedrijven op strategisch niveau besluiten om over te stappen op 3D-printen omdat ze dan lokaal kunnen produceren. Zelfs de olie- en gasindustrie, waar hoge eisen aan materialen worden gesteld, willen overstappen.
Een voorbeeld uit eigen land is te vinden bij Biggelaar Special Performance in Oisterwijk. Het Brabantse bedrijf is gespecialiseerd in het tunen en restaureren van Ducati motoren. Voor een Ducati 998 RS racemotor uit 2001 bleek een kritisch onderdeel van de carburateur niet meer leverbaar. Het oorspronkelijk metalen onderdeel, omdat de temperatuur oploopt tijdens het racen, is geredesignd en wordt nu ge-3D-print met Novamid ID1020-CF, een filament van DSM dat met koolstofvezels is versterkt. Het blijkt niet alleen mechanisch voldoende sterk te zijn, maar eveneens bestand tegen de hoge temperaturen tijdens een race met de motor. Van den Biggelaar en DSM ontwikkelen nu de volgende versie: ze willen de rubberen afdichtringen voortaan eveneens meeprinten.