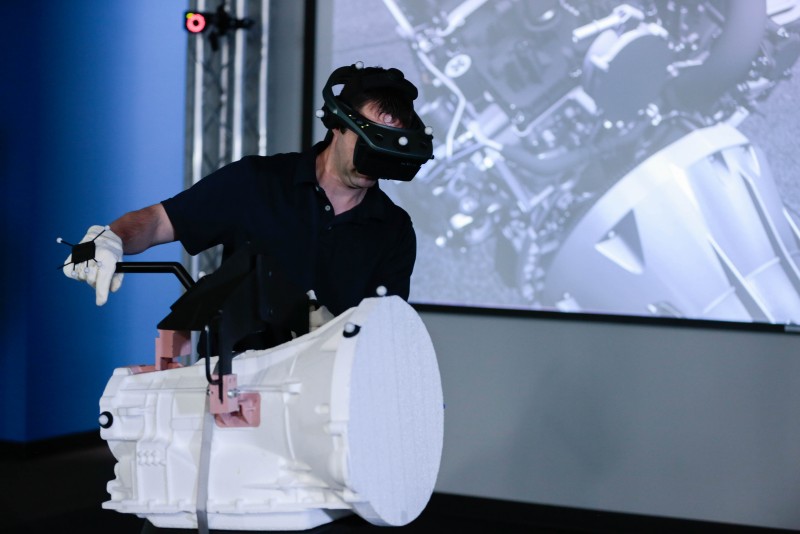
Sinds 2003 is letsel van werknemers aan de productielijn van Ford in de VS met 70 procent afgenomen. Dit resultaat is bereikt door gebruik te maken van nieuwe ergonomische technologieën zoals virtuele productie van een nieuwe auto, aldus Ford.
Elke beweging die de productiemedewerker moet maken wordt daarbij bestudeerd. Speciale apparaten die de te assembleren voertuigen draaien en op de ideale werkhoogte brengen voor de assemblagemedewerker en herontwerp van werkstations worden met behulp van een data-gedreven proces ontwikkeld.
Minder vermoeiend
Twee tot drie jaar voorafgaand aan de introductie van een nieuw voertuig, simuleert Ford het montageproces met behulp van zowel menselijke als virtuele proefpersonen om de fysieke arbeid die nodig is om een voertuig te bouwen te beoordelen. De verzamelde gegevens worden gebruikt om technische oplossingen te bedenken om taken op de werkvloer minder vermoeiend en belastend in te kunnen richten. Er wordt gebruik gemaakt van drie belangrijke technologieën om gegevens te verzamelen: scannen van lichaamshouding en -beweging, 3D-printen en virtuele realiteit.
Virtual reality systeem
Het full-body motion capture (scannen lichaamshouding en -beweging) systeem maakt gebruik van meer dan 52 motion-capture sensoren die op het lichaam van een werknemer zijn geplaatst om lichaamsbewegingen te monitoren en om spierkracht, zwakte en lichaamsonbalans te evalueren. Het virtual reality-systeem maakt gebruik van 23 motion capture camera’s en een virtual reality-bril om een werknemer in een virtuele werkomgeving te plaatsen en taakhaalbaarheid en -vaardigheid te evalueren. Het derde proces, het 3D-printing systeem, maakt gebruik van 3D-geprinte replica onderdelen om de benodigde vrije ruimte voor de hand te helpen controleren in het assemblageproces. Elk biedt essentiële gegevens die worden gebruikt om de algehele veiligheid van het assemblageproces voor medewerkers te evalueren.